Apa itu Mesin Punch Pneumatik?
Mesin punch press pneumatik adalah alat mesin otomatis yang dilengkapi dengan sistem kontrol programmable, digunakan untuk memproses berbagai komponen lembaran logam. Dengan efisien, ia menyelesaikan beberapa operasi perforasi kompleks dan peregangan dangkal dalam satu siklus, secara otomatis memproses lubang dengan bentuk dan dimensi yang berbeda sesuai kebutuhan. Memahami prinsip kerja, metode pemrosesan, teknik seleksi, panduan operasional, dan esensi perawatan dari punch press pneumatik sangat penting.
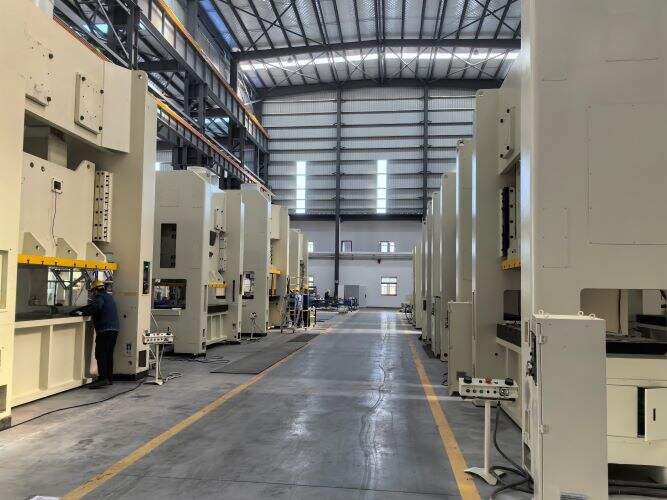
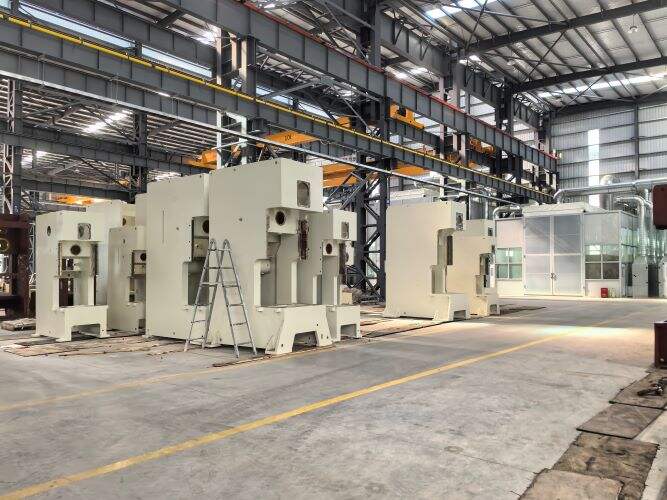
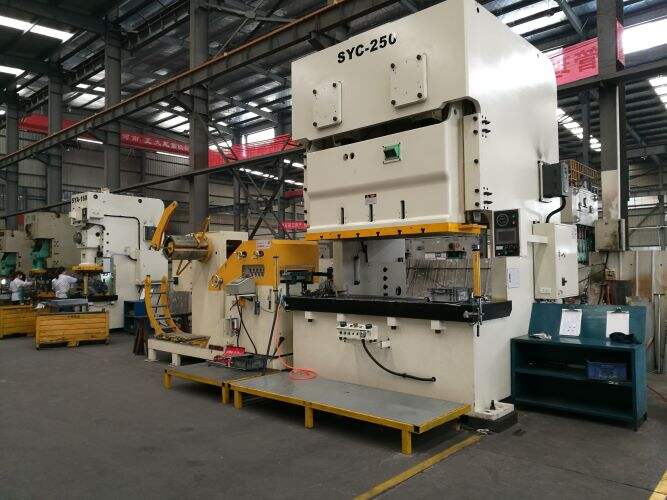
Prinsip Kerja Punch Press Pneumatik
Prinsip desain dari punch press pneumatik melibatkan konversi gerakan rotasi menjadi gerakan linear. Output utama didorong oleh motor listrik utama, yang menggerakkan flywheel. Kopling kemudian menghubungkan gigi, poros engkol (atau gigi eksentrik), batang penghubung, dan komponen lainnya, mencapai gerakan linear dari slidenya. Gerakan dari motor listrik utama ke batang penghubung melibatkan gerakan melingkar.
Pemotong pneumatik menerapkan tekanan pada benda kerja untuk menyebabkan deformasi dan mencapai bentuk serta ketelitian yang diinginkan. Proses ini memerlukan kolaborasi antara satu set cetakan (atas dan bawah) di mana material ditempatkan. Gaya yang diterapkan pada material selama pemrosesan diserap oleh bagian mekanis dari pemotong pneumatik, menghasilkan gerakan mesin dan produksi bagian tersebut.
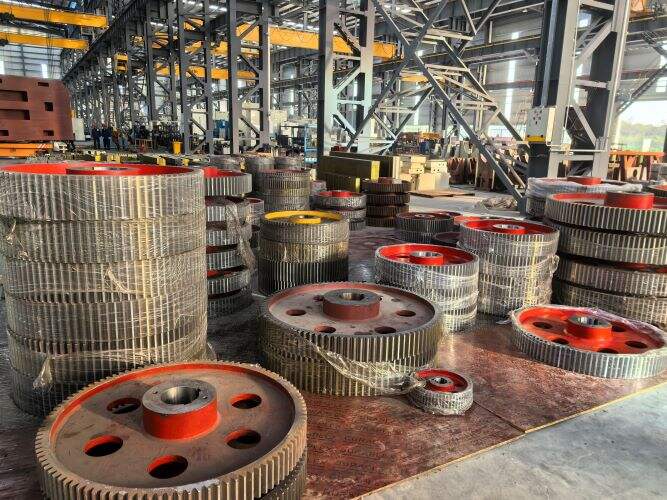
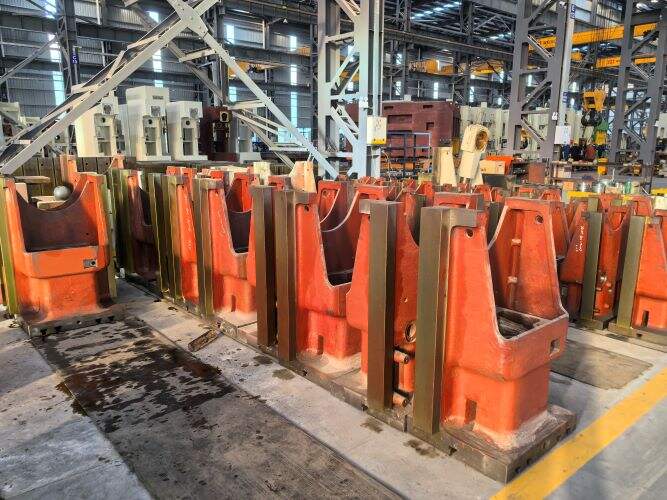
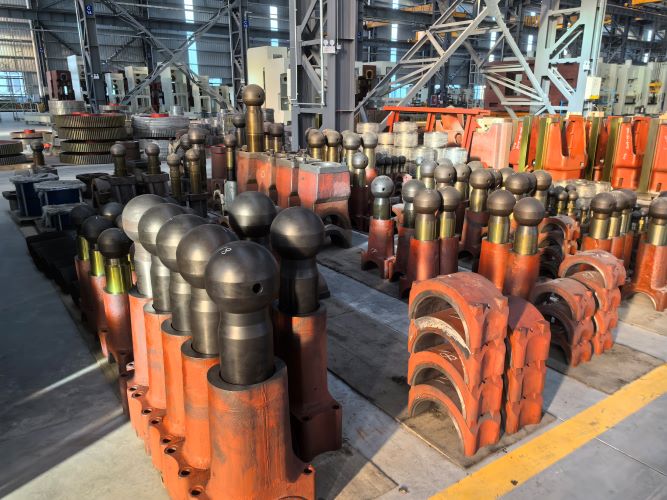
Metode Pemrosesan Pemotong Pneumatik
1. Langkah Tunggal: Menyelesaikan operasi pemotongan tunggal, termasuk distribusi linier, distribusi busur, distribusi lingkar, dan pemotongan lubang grid.
2. Pemotongan Kontinu dalam Arah Sama: Menggunakan metode tumpukan dengan cetakan berbentuk persegi panjang untuk memproses lubang panjang, memotong tepi, dan lainnya.
3. Pemotongan Kontinu dalam Beberapa Arah: Menggunakan cetakan yang lebih kecil untuk memproses lubang yang lebih besar.
4. Nibbling: Menggunakan cetakan bulat kecil untuk memotong secara berturut-turut dan membentuk busur.
5. Pembentukan Tunggal: Peregangan dangkal satu kali berdasarkan bentuk cetakan.
6. Pembentukan Kontinu: Lebih besar dari cetakan standar, digunakan untuk proses pembentukan seperti lubang angin standar besar, embossing, dan pembentukan tangga.
7. Pembentukan Array: Memproses beberapa bagian kerja yang identik atau berbeda pada lembaran besar.
Teknik Pemilihan untuk Mesin Punch Pneumatik
1. Pertimbangkan panjang, ketebalan bahan, hasil produksi, dan ruang tersedia saat memilih mesin punch pneumatik untuk kebutuhan tertentu.
2. Evaluasi apakah fitur tambahan, seperti gerobak koil untuk memudahkan pemuatan atau sistem kontrol loop untuk manajemen tegangan, diperlukan untuk aplikasi tersebut.
Pedoman Keamanan Operasional untuk Mesin Punch Pneumatik
1. Pastikan colokan daya untuk badan mesin dan kotak kontrol tidak melebihi beban yang ditentukan.
2. Sebelum operasi, periksa pelumasan bagian bergerak dan inspeksi kopling dan rem untuk memastikan fungsi yang tepat.
3. Selama penggantian mati, tutup sumber daya, pastikan mesin berhenti sepenuhnya, dan baru kemudian pasang serta sesuaikan matinya.
4. Sebelum memulai mesin punch pneumatik, pastikan area kerja bebas dari orang dan kotoran.
5. Selama operasi mesin, hindari memasukkan tangan ke area kerja, dan jangan pernah menangani atau mengeluarkan benda kerja secara manual.
6. Tombol pemberhentian darurat harus digunakan ketika memberi makan secara manual atau membantu dalam proses pemberian makan selama proses punching.
7. Jika suara aneh atau kerusakan mekanis terdeteksi, segera matikan daya dan lakukan pemeriksaan menyeluruh.
Tips Perawatan untuk Mesin Punch Pneumatik
1. Jaga kolom pusat dan panduan slider tetap bersih untuk mencegah goresan dan menjaga kebersihan platform saat pemasangan mati.
2. Oleskan pelumas pada flywheel dan feeder setiap bulan dengan grease untuk kinerja mesin yang optimal.
Ganti minyak mesin (minyak mesin 32# atau Mobil 1405#) dalam bulan pertama penggunaan dan setiap enam bulan kemudian untuk memastikan operasi normal dan presisi.
Memahami aspek-aspek ini dari punch press pneumatik sangat penting untuk memaksimalkan efisiensi, keamanan, dan umur panjang peralatan dalam berbagai aplikasi pekerjaan logam.