Apa itu Punch Press Pneumatik?
Mesin tekan punch pneumatik adalah alat mesin automatik yang dilengkapi dengan sistem kawalan boleh diprogram, digunakan untuk memproses pelbagai komponen lembaran logam. Ia secara cekap menyelesaikan pelbagai pengeboran kompleks dan operasi peregangan dangkal dalam satu kitaran, secara automatik memproses lubang dengan bentuk dan saiz berbeza mengikut keperluan. Memahami prinsip kerja, kaedah pemprosesan, teknik pemilihan, panduan operasi, dan asas pemeliharaan mesin tekan punch pneumatik adalah sangat penting.
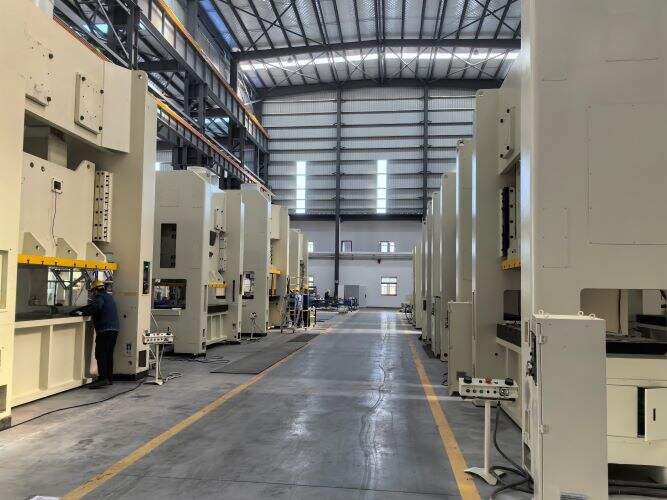
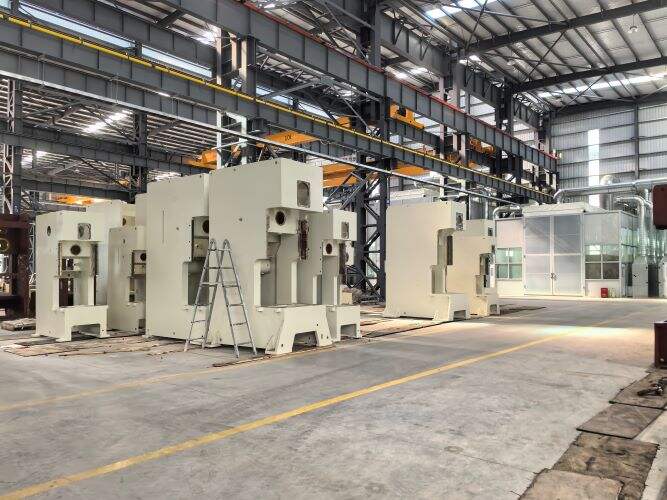
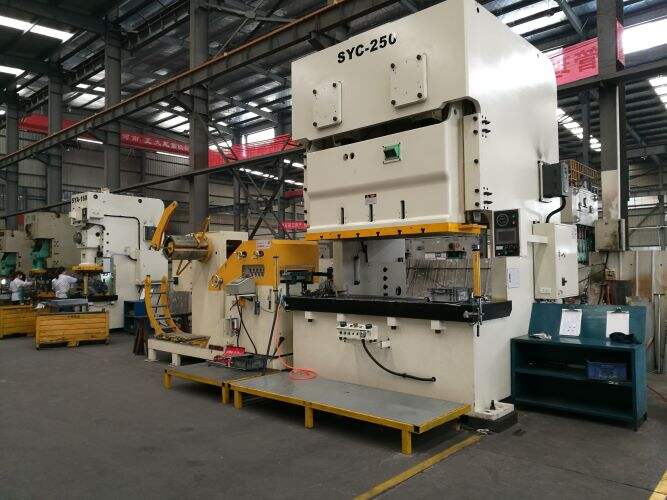
Prinsip Kerja Mesin Tekan Punch Pneumatik
Prinsip reka bentuk mesin tekan punch pneumatik melibatkan penukaran gerakan putaran kepada gerakan linear. Output utama dipacu oleh motor elektrik utama, yang menggerakkan roda terbang. Clutch pada gilirannya menggerakkan gear, poros engkol (atau gear eksentrik), rod penghubung, dan komponen lain, mencapai gerakan linear bagi slaid. Gerakan dari motor elektrik utama ke rod penghubung melibatkan gerakan bulat.
Mesin punch pneumatik menerapkan tekanan pada bahan kerja untuk menyusutkannya, mencapai bentuk dan ketepatan yang diinginkan. Proses ini memerlukan kerjasama satu set cetakan (atas dan bawah) di antara mana bahan diletakkan. Daya yang diterapkan kepada bahan semasa pemprosesan diserap oleh badan mekanikal mesin punch pneumatik, menghasilkan gerakan mesin dan pengeluaran bahagian.
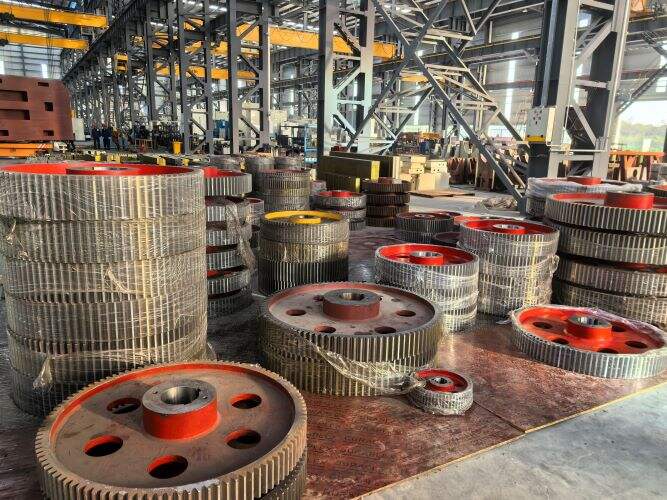
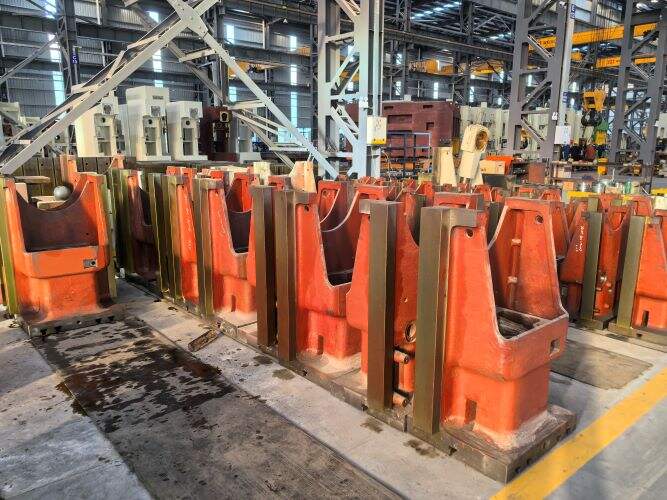
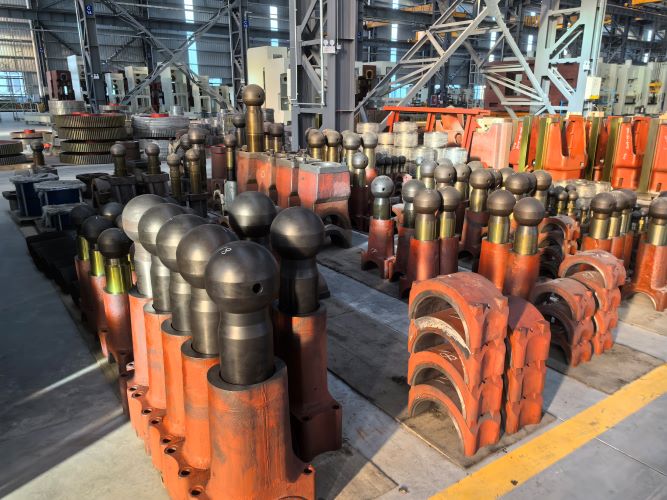
Kaedah Pemprosesan Mesin Punch Pneumatik
1. Langkah Tunggal: Menyempurnakan operasi punch tunggal, termasuk taburan linear, taburan lengkung, taburan lilitan, dan pengecap lubang grid.
2. Penjagaan Berterusan dalam Arah Sama: Menggunakan kaedah tumpukan dengan cetakan segi empat untuk memproses lubang panjang, memotong tepi, dan lain-lain.
3. Penjagaan Berterusan dalam Pelbagai Arah: Menggunakan cetakan kecil untuk memproses lubang besar.
4. Nibbling: Menggunakan cetakan bulat kecil untuk mengecap dan membentuk lengkung secara berturut-turut.
5. Pembentukan Tunggal: Peregangan dangkal satu kali berdasarkan bentuk die.
6. Pembentukan Berterusan: Lebih besar daripada die piawai, digunakan untuk proses pembentukan seperti lubang angin piawai besar, penampalan, dan langkah pembentukan.
7. Pembentukan Array: Memproses beberapa kerjaan yang sama atau berbeza pada lembaran besar.
Teknik Pemilihan untuk Punch Press Pneumatik
1. Pertimbangkan panjang, ketebalan bahan, output pengeluaran, dan ruang yang tersedia apabila memilih punch press pneumatik untuk keperluan tertentu.
2. Nilaikan sama ada ciri tambahan seperti troli pita untuk memudahkan pemuatan atau sistem kawalan loop untuk pengurusan tegangan diperlukan untuk aplikasi tersebut.
Pedoman Keselamatan Operasi untuk Punch Press Pneumatik
1. Pastikan soket kuasa untuk badan mesin dan kotak kawalan tidak melebihi beban yang ditentukan.
2. Sebelum operasi, periksa pelumasan bahagian bergerak dan semak clutch dan brek untuk fungsi yang betul.
3. Semasa penggantian die, tutup bekalan kuasa, pastikan mesin berhenti sepenuhnya, dan barulah pasang dan tukar die.
4. Sebelum memulakan penjimbaran pneumatik, pastikan kawasan kerja bebas daripada orang dan kotoran.
5. Semasa operasi mesin, elakkan memasukkan tangan ke dalam kawasan kerja, dan jangan pernah menangani atau mengeluarkan bahan secara manual.
6. Butang henti kecemasan mestilah digunakan apabila memberi makan secara manual atau membantu memberi makan semasa proses penjimbaran.
7. Jika bunyi yang tidak normal atau gangguan mekanikal dikesan, matikan kuasa dengan segera dan lakukan pemeriksaan menyeluruh.
Tips Penyelenggaraan untuk Punch Press Pneumatik
1. Kekalkan tiang pusat dan panduan slaid bersih untuk mengelakkan garisan dan memastikan kebersihan platform semasa pemasangan die.
2. Lorekkan pelincir kepada flywheel dan feeder sekali sebulan untuk prestasi mesin yang optimum.
Tukar minyak mesin (minyak mekanikal 32# atau Mobil 1405#) dalam tempoh satu bulan pertama penggunaan dan seterusnya setiap enam bulan untuk memastikan operasi normal dan kejituan.
Memahami aspek-aspek ini tentang punch press pneumatik adalah perkara penting untuk memaksimumkan kecekapan, keselamatan, dan umur peralatan dalam pelbagai aplikasi kerja logam.