Seria SPL Ultra-Cienka Precyzyjna Maszyna Prostująca: Maszyna do Wyrównywania Rozwinięć Metalowych Dla Grubości Materiału Od 0,08mm - 0,3mm
Udostępnij
Do ciągłego wycinania materiałów o różnych grubościach
Pracuje w parze z maszyną rozwinąć materiału do produkcji automatycznej
Może być dostosowane
Opis produktu
Funkcja:
1. Ta seria maszyn do wyprostowywania jest ulepszoną wersją maszyny do wyprostowywania serii H naszej firmy, specjalnie zaprojektowanej do precyzyjnego ciosu cienkich materiałów. Jak wiadomo, niemożliwe jest uzyskanie dobrych produktów bez wyrównania koca i eliminacji naprężeń, dlatego wydajność maszyny do wyprostowywania odgrywa kluczową rolę w produkcji.
2. Walce wyrównujące i pomocnicze tej maszyny są wykonane z importowanego materiału SUJ2, poddano go obróbce cieplnej do twardości HRC60. Po wypolerowaniu dokonuje się dalszego ich przetwarzania poprzez galwanizację chromową, aby zapewnić jednolity warstwę chromu oraz dokładność kształtu każdego wału.
3. Dostosowanie wyrównania tej maszyny opiera się na zmiennym urządzeniu do precyzyjnej regulacji równowagi czteropunktowej, wyposażonym w manometr, który pozwala szybko określić punkt wyrównania.
4. Każdy wyprostowywalnik serii S ma wbudowane pomocnicze walce wyrównujące, które gwarantują, że podczas procesu produkcyjnego nie ulegają one deformacji gięciowej, co poprawia jakość płaskości produktów.
5. Poniższe walce pomocnicze są stałe, co zwiększa sztywność dolnych wałków i uniemożliwia ich deformację pod wpływem naprężeń.
6. Górne wałki pomocnicze są podwieszone, co umożliwia stosowanie różnej presji w zależności od potrzeb, aby wzmacniać siłę wyrównującą i zwiększać czas użytkowania wyrównujących wałków oraz poprawiać wymagania dotyczące płaskości powierzchni materiału arkusznego.
7. Zębatki napędowe mają zastosowanie wymuszonego obiegu oleju smarującego, co zmniejsza zużycie zębów i pozwala na długoterminowe działanie przy wysokich temperaturach.
8. Mechanizm napędowy niezależnie steruje każdym wałkiem prostującym synchronicznie, co redukuje skumulowane tolerancje odstępu spowodowane transmisją zębatkową i poprawia wymagania dotyczące płaskości materiału arkusznego.
9. Dodanie systemu smarowania przedłuża żywotność maszyny i pozwala jej działać w stabilnych warunkach przez długi czas.
10. Ze względu na różnice w materiale, szerokości i grubości paska, nie ma jednolitej odniesienia liczbowego. Dlatego zaleca się spróbowanie wyprostowania małej części materiału przed masową produkcją, a kontynuowanie produkcji tylko wtedy, gdy osiągnięto pożądane wyniki.
Wprowadzenie:
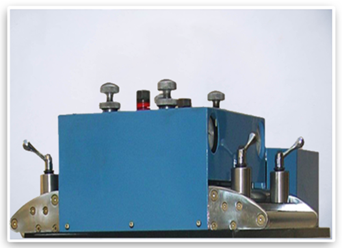
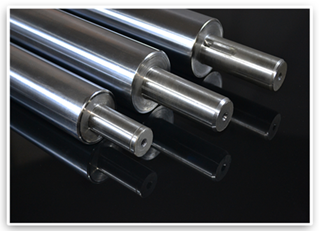
·Głowica Wyprostowująca
1. Głowa maszynowa posiada konstrukcję z równoległymi wałkami, łącznie 23 wałki wyprostowujące, 11 po stronie górnej i 12 po stronie dolnej.
2. Zastosowano cztero-punktowe drobne dostosowywanie, co jest bardziej odpowiednie do przetwarzania produktów o wysokiej precyzji. Regulacja ciśnienia czterech niezależnych kołek podajników służy do ładowania i rozładunku, skutecznie zapobiegając odchyleniom i deformacjom materiału.
3. Wałek podtrzymujący materiał wykonany jest z galwanizowanego wałka bez napędu, z całościowym formowaniem materiału. Powierzchnia jest odporna na drapania i zużycie, a obroty są gładkie i trwałe dzięki mechanicznym łożyskom.
4. Koło ręczne jest wykonane z żelaza litniczego i poddane jest elektroplatynowaniu powierzchni, reprezentując najbardziej tradycyjny typ koła ręcznego.
5. Osłony ochronne są montowane po obu stronach części przekazującej dla ochrony, wyposażone w okna obserwacyjne ułatwiające obserwację.
·Walce wyprostowujące
1. Walce wyprostowujące są wykonane z stalowego wału nałożonego, poddawane grubej elektroplatynie po przetworzeniu częstotliwości średniej, co zapewnia twardość powierzchni nie mniejszą niż HRC58, gwarantując trwałość.
2. Stalowa rura kolista jest kucona z GCr15, a następnie poddana przetwarzaniu wstępno-grzewemu (analitycznemu), obróbce skrawaniem, frezowaniu, przetwarzaniu częstotliwości średniej, szlifowaniu wstępному, stabilizacji zimnej i wreszcie precyzyjnemu szlifowaniu. Ten proces maksymalizuje precyzję, stężenie osiowe, gładkość i twardość, przedłużając żywotność wałków wyprostowujących.
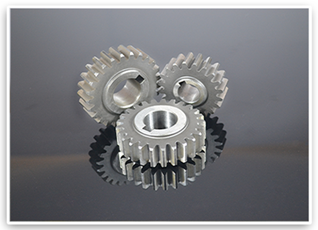
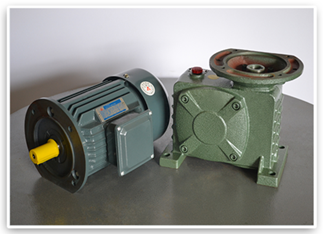
·Ząb przekazywania
Proces produkcji biegów obejmuje następujące etapy: wstępne obróbki mechaniczne biegów, obróbka powierzchni biegów, obróbka cieplna oraz wypolerowanie powierzchni biegów. W ramach wstępnego obrabiania stosuje się wykucia, które przechodzą normalizację w celu poprawy ich obrabialności, ułatwiając wycinanie. Według rysunku projektowego biegów przeprowadza się wstępne obróbki, po których następują półkońcowe operacje takie jak torno, skrawanie i struganie zębów, aby osiągnąć podstawowe kształty biegów. Następnie przeprowadza się obróbkę cieplną w celu poprawy właściwości mechanicznych. Zgodnie z specyfikacjami projektowymi na rysunku wykonuje się końcową precyzyjną obróbkę, dopracowując geometrię i dokładność biegów. Dzięki tym procesom nasze biegi osiągają klasę 6, charakteryzując się wysoką odpornością na zużycie, siłą i długim okresem użytkowania.
·Sekcja mocy
1. Przyjęto 80-rodzajowy pionowy reduktor ślimakowy, wykorzystując przekształtnik prędkości bieżnika, aby zmniejszyć prędkość obrotową silnika do pożądanego poziomu i osiągnąć mechanizm o większym momentu obrotowego.
2. Używając pionowego silnika, z niskim poziomem drgań i hałasu, część statora wykonana jest z czystych miedzianych cewek, co daje żywotność dziesięć razy dłuższą niż w przypadku zwykłych cewek. Wyposażony w kulkowe podwójne łożyska, co prowadzi do niskiego tarcia i temperatury.
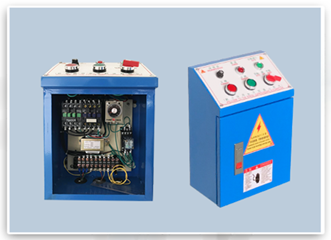
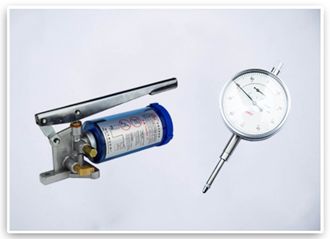
·Pudełko sterowania elektrycznego
1. Korzystanie z relé z legity aliancu, pełnych miedzianych cewek, ogniotrwałej podstawy bezpieczeństwa, zapewniających trwałość na długi okres.
2. Stosowanie regulowanego relé opóźnienia zabezpieczenia, z kontaktami z legity aliancu, z wieloma opcjami skali, spełniającymi różne zakresy opóźnień.
3. Przełączniki mają kontakty suwne z funkcją samoczyszczącą. Kontakty normalnie otwarte i zamknięte używają osobnej izolowanej struktury, umożliwiającą dwubiegunowe działanie, z pozycjonowaniem antyrotaacyjnym i amortyzującymi nakładkami zabezpieczającymi przed luźnościami.
4. Używanie przycisków samonastawnych, lekkich z umiarkowanym wyciągiem klucza. Wykorzystanie modularnej struktury, punkty kontaktowe korzystają z materiałów złożonych na bazie ketonu, zapewniając silną przewodność i zdolność przenoszenia dużych prądów, z życiem produkcyjnym do 1 miliona cykli.
·Wskazówka analogowa, pompa olejowa
1. Korzystanie z manualnej pompy tłocznej do szybkiej i oszczędnej dostawy oleju, z importowanymi uszczelnikami tłokowymi, aby zapobiec wycieku oleju oraz importowanymi sprężynami odpornymi na deformację i starzenie.
2. Użycie wskaźnika analogowego z stalowego wykonania z precyzyjnym licznikiem, szkłem chroniącym przed pyłem, wewnętrznie wyłożonym rękawem miedzianym, a także zastosowanie ruchu wykonanego z miedzi, co zapewnia stabilną konstrukcję i dokładne pomiary.
Parametr:
Model | SPL-100 | SPL-200 |
Maks. szerokość | 100mm | 200mm |
Grubość | 0,08~0,3mm | 0,08~0,3mm |
Prędkość | 15 minut na minutę | 15 minut na minutę |
Silnik | 0,5KM×4P | 1HP×4P |
Średnica wału roboczego | Φ12 | Φ12 |
Ilość wałków roboczych | 11/12(Górny/Dolny) | 11/12(Górny/Dolny) |
Wymiary | 0.7×0.6×1.3m | 0.8×0.6×1.3m |