CL Series Straightener Cum Uncoiler 2 in 1 for Sheet Thickness: 0.4mm~2.2mm
Share
Uncoiler/sraightener machine
Save space
High precision
Product Description
Straightener Cum Decoiler
Cradle type decoiler cum straightener.
Instead of utilizing an expandable mandrel, the coil is positioned on driven rollers within the coil cradle. These rollers come equipped with adjustable side plates to ensure proper centering. Optionally, side rollers can be added to the side plates to protect delicate coils from damage along their edges.
Specification:
Features
1. The integrated material rack and straightening machine occupy minimal space and are commonly used.
2. Suitable for correcting the flatness and feeding of various metal coils.
3. Can be equipped with a special infinitely variable speed device to control the feeding speed as needed.
4. The material rack and straightening machine are integrated into one unit, with chain drive and chrome-plated rollers. Equipped with a special infinitely variable speed device to control feeding speed, ensuring durability.
5. Material feeding is achieved by clamping the material with side plates on both sides, driven by feeding rollers, and the speed is controlled by the leveling section.
6. The leveling rollers are made of chrome steel 40CR, treated with tempering, high-frequency quenching, and hard chrome plating. With a surface hardness of HRC60 degrees and a chrome plating thickness of 0.05mm on one side, they are highly durable.
7. Leveling adjustment adopts a four-point independent micro-adjustment, controlled by a scale ruler for simplicity and practicality.
8. The L-shaped iron frame induction rack is mainly suitable for lightweight and small materials with low surface requirements in stamping production. It is often used in conjunction with pneumatic feeders to form an economical stamping automation production line.
Structure
·The head of straightener
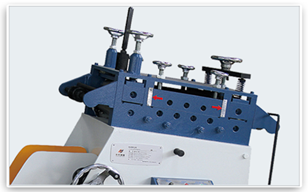
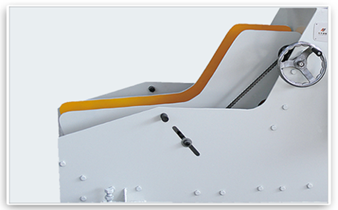
1. The machine head adopts a parallel roller design, with a total of 7 straightening rollers (3 on the top and 4 on the bottom).
2. Four-point micro-adjustment is employed, making it more suitable for processing high-precision products. Four-point independent pressure adjustment is used for feeding and unloading to effectively prevent material deviation and deformation.
3. The material support rollers are made of passive galvanized rollers, integrally formed, with a surface that is resistant to scratches and wear. They utilize mechanical bearings, providing flexible and durable rotation.
4. Cast iron handwheels are used, with a surface electroplated for traditional aesthetics.
5. Protective covers are installed on both sides of the transmission part for protection, equipped with viewing windows for convenient observation.
·Rack section
1. This equipment adopts an integrated design of material rack and straightening unit, maximizing space utilization.
2. The material rack is designed with a cantilever beam, and all frame plates are cut with laser or plasma cutting, ensuring high precision and good equipment interchangeability.
3. All parts are processed using numerical control (NC) and computer numerical control (CNC), ensuring good interchangeability.
4. The overall structure is simple, and assembly and replacement of equipment parts can be performed by general technical workers, making it convenient, fast, and greatly reducing maintenance costs.
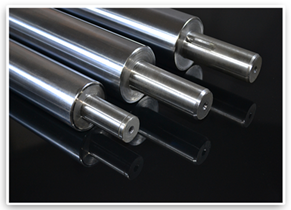
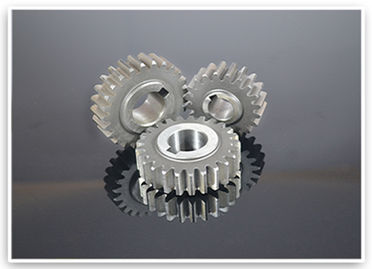
·Straightener roller
1. The straightening rollers are made of solid bearing steel, undergo mid-frequency treatment followed by thickened electroplating, ensuring a surface hardness of no less than HRC58 to guarantee material durability.
2. GCr15 forged round steel is employed, subjected to pre-heat treatment (spheroidizing annealing), followed by turning, milling, mid-frequency treatment, rough grinding, cold stabilization, precision grinding, and finally electroplating. This process maximizes precision, concentricity, smoothness, and hardness, thereby extending the service life of the straightening rollers.
·Drive gear
The gear machining process includes the following steps: gear blank processing - tooth surface machining - heat treatment - tooth surface grinding.
The gear blank is mainly forged and then subjected to annealing to improve its machinability for easier cutting.
Following the gear design drawings, rough machining is conducted, followed by semi-precision machining, involving turning, milling, and hobbing to achieve basic gear formation. Subsequently, heat treatment is performed to enhance mechanical properties. According to the design requirements, final precision machining is carried out, refining the reference surface and gear profile. Through these processes, our gears can achieve a grade of 6, with high wear resistance, high strength, and long service life.
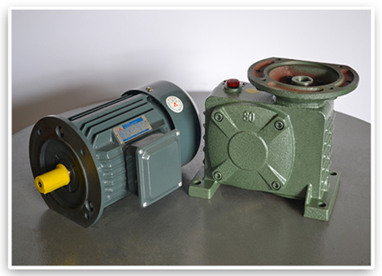
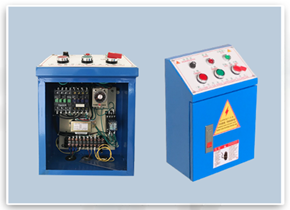
·Power section
1. Utilizing the 80-type worm gear vertical reducer, this gearbox employs the speed converter of gears to reduce the rotational speed of the motor (engine) to the desired speed while obtaining a mechanism with increased torque.
2. Equipped with a vertical motor, featuring low vibration and noise levels, the stator section employs pure copper coils with a lifespan ten times that of ordinary coils. Ball bearings are installed at both ends, reducing friction and maintaining low temperatures.
·Electric control box
1. Utilizing silver alloy relays with all-copper coils and flame-retardant safety bases, ensuring long-lasting durability.
2. Employing safety protection adjustable circuit delay relays, with silver alloy contacts, multiple adjustment dials, catering to various delay ranges.
3. Switches feature sliding contact design with self-cleaning function. Normally open and normally closed contacts utilize a separate insulated structure, allowing for bipolar operation and equipped with anti-rotation positioning and anti-loosening mounting pads.
4. Utilizing self-resetting push buttons with light force and moderate stroke. The contacts adopt a modular combination structure with ketone-based composite points, providing strong conductivity, capable of carrying large currents, and boasting a lifespan of up to 1 million cycles.
Model |
CL-150 |
CL-200 |
CL-250 |
CL-300 |
Material width |
150mm |
200mm |
250mm |
300mm |
thickness |
0.4~2.2mm |
|||
Coil outer diameter |
800mm |
|||
Coil weight |
350kg |
400kg |
500kg |
500kg |
speed |
15m/min |
|||
motor |
1/2hp/4p |
1hp/4p |
1hp/4p |
1hp/4p |