GO-B Series Straightener Cum Uncoiler 2 in 1 Metal Coil Feeding System for Sheet Thickness: 0.1mm~0.8mm
Share
Uncoiler/sraightener machine
Save space
High precision
Product Description
Straightener Cum Decoiler
Features
1. Integrating the frame and straightening machine reduces installation space, minimizing transitional stages during precision material straightening, and maximizing machine performance.
2. The frame and straightening machine are controlled separately with independent control cabinets, each equipped with a frequency converter, ensuring smooth operations and providing more effective protection for the machines, preventing deformation or distortion caused by external forces during operation.
3. Both machines utilize universal joint transmission and full gear transmission, effectively preventing passive rotation of the upper rollers and potential material damage.
4. Equipped with dial indicators on the wheels, facilitating quick location of leveling points.
5. The addition of backpressure wheels enhances the rigidity of the straightening rolls, resulting in superior straightening effects.
6. The addition of system components increases the machine's lifespan.
7. The power for material rack straightening is separated and controlled independently with frequency converters, effectively preventing secondary material deformation and improving the quality of stamped products.
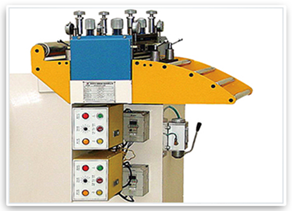
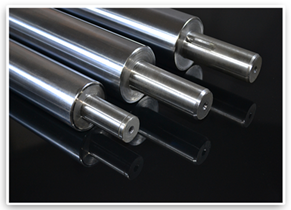
·Straightener head
1. The machine head adopts a parallel roller design, with a total of 7 straightening rollers (3 on the top and 4 on the bottom).
2. Utilizing four-point micro-adjustment, it is more suitable for processing high-precision products. The feeding and unloading processes employ four-point independent pressure adjustment on the feeding wheel, effectively preventing material deviation and deformation.
3. The material support rollers are made of passive galvanized rollers, integrally formed, with a surface resistant to scratches and wear. They use mechanical bearings, providing flexible and durable rotation.
4. Cast iron handwheels are used, with a surface electroplated for traditional aesthetics.
5. Protective covers are installed on both sides of the transmission part for protection, equipped with viewing windows for convenient observation.
·Straightening roller
1. The straightening rollers are made of solid bearing steel, undergo mid-frequency treatment followed by thickened electroplating, ensuring a surface hardness of not less than HRC58 to guarantee material durability.
2. GCr15 forged round steel is used, which undergoes pre-heat treatment (spheroidizing annealing), followed by turning, milling, mid-frequency treatment, rough grinding, cold stabilization, precision grinding, and finally electroplating. This process maximizes precision, concentricity, smoothness, and hardness, thereby extending the service life of the straightening rollers.
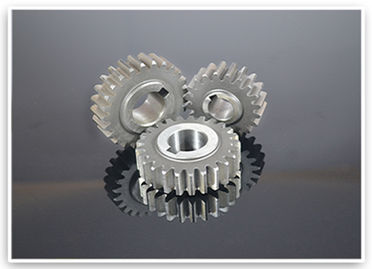
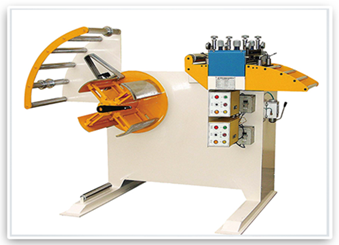
·Drive gear
The gear machining process includes the following steps: gear rough machining - tooth surface machining - heat treatment - tooth surface grinding. Rough machining primarily involves forging, followed by annealing to enhance its machinability, facilitating cutting. According to the gear design drawings, rough machining is performed, followed by semi-precision machining involving turning, milling, and hobbing to achieve basic gear formation. Subsequently, heat treatment is conducted to improve mechanical properties. Following the design requirements in the drawings, final precision machining is carried out, refining the reference surface and gear profile. Through these processes, our gears can achieve a grade of 6, with high wear resistance, high strength, and long service life.
·Frame part
1. This equipment adopts an integrated design of material rack and straightening unit, enhancing site utilization.
2. The material rack is designed with a cantilever beam, and all frame plates are cut with laser or plasma cutting, ensuring high precision and good equipment interchangeability.
3. All parts are processed using numerical control (NC) and computer numerical control (CNC), ensuring good interchangeability.
4. The overall structure is simple, and assembly and replacement of equipment parts can be performed by general technical workers, making it convenient, fast, and greatly reducing maintenance costs.
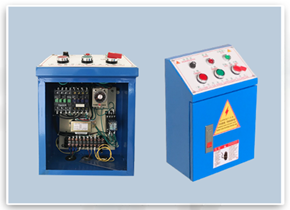
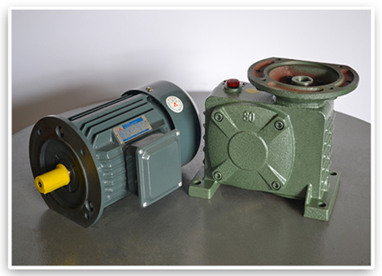
·Electric control box
1. Utilizing silver alloy relays with all-copper coils and flame-retardant safety bases, ensuring long-lasting durability.
2. Employing safety protection adjustable circuit delay relays, with silver alloy contacts, multiple adjustment dials, catering to various delay ranges.
3. Switches feature sliding contact design with self-cleaning function. Normally open and normally closed contacts utilize a separate insulated structure, allowing for bipolar operation and equipped with anti-rotation positioning and anti-loosening mounting pads.
4. Utilizing self-resetting push buttons with light force and moderate stroke. The contacts adopt a modular combination structure with ketone-based composite points, providing strong conductivity, capable of carrying large currents, and boasting a lifespan of up to 1 million cycles.
·Power part
1. Employing an 80-type worm gear vertical reducer, this setup utilizes the gear's speed converter to reduce the rotational speed of the motor (engine) to the desired speed, while obtaining a mechanism with increased torque.
2. Using a vertical motor, characterized by low vibration and noise levels. The fixed rotor section features pure copper coils with a lifespan ten times that of standard coils. Ball bearings are installed at both ends, minimizing friction and maintaining low temperatures.
Specification:
Type | GO-200B | GO-300B | GO-400B | GO-500B | GO-600B |
Max.width | 200mm | 300mm | 400mm | 500mm | 600mm |
Thickness | 0.1-0.8mm | ||||
Coil.I.Dia | 450-530mm | ||||
Coil.O.Dia | 1200mm | ||||
Max.weight | 800kg | 1000kg | 1500kg | 1500kg | 2000kg |
Straight Power | 1/2HP | 1HP | 2HP | 2HP | 3HP |
UncoilPower | 1HP | 1HP | 2HP | 2HP | 3HP |
Straight adjust | 4 point worm gear fine adjsutment | ||||
Max.speed | 15m/min | ||||
Expansion method | Manual | ||||
Loop control | Touch sensor |