HS Series Thick Plate Straightening Machine: Metal Sheet Coil Leveling For Material Thickness Range Of 1.6mm - 6.0mm
Share
For different thickness material continuous punching use
Work together with uncoiler machine for automatic production
Can be customized
Product Description
Features:
1.The correction wheel is made of solid bearing steel, undergoes high-frequency heat treatment, is ground and hard chrome-plated, and after calibration by the machine, it is smooth and free of pressure marks, without damaging the material surface.2
2. The machine can be used independently and can also be used together with the MT-type and DBMT-type automatic feeding racks, resulting in good performance.
3. The machine adopts a large-size cylinder for material pressing, and correction adjustment is carried out using synchronized worm and worm gear adjustment. With one rotation of the handle, the upper wheel of correction only descends 1mm for fine adjustment.
Introduction:
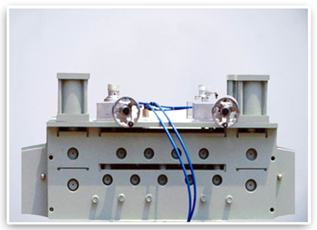
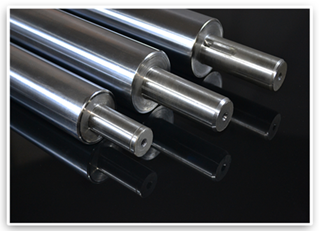
·The head of straightener
1. The machine head adopts a parallel roller design, with a total of 9 precision correction rollers, 4 on the upper side and 5 on the lower side.
2. Equipped with a large-size cylinder for material pressing, it is more suitable for processing high-precision products. The correction adjustment is carried out using synchronized worm and worm gear adjustment, effectively preventing material deviation and deformation.
3. The material support rollers are made of non-powered galvanized rollers, integrally formed, with a surface resistant to scratching and abrasion. They use mechanical bearings, allowing flexible rotation and long-lasting durability.
4. It features a cast iron handwheel with a surface electroplating treatment, representing the most traditional type of handwheel.
·Straightener roller
1. The correction roller is made of solid bearing steel, undergoes thick electroplating treatment after medium-frequency processing, ensuring a surface hardness not less than HRC58 to guarantee material durability.
2. Made of GCr15 forged round steel, it undergoes pre-heating treatment (spheroidizing annealing), followed by turning, milling, medium-frequency processing, rough grinding for cold stabilization, precision grinding, and finally electroplating. This maximizes precision, concentricity, smoothness, and hardness, extending the service life of the correction roller.
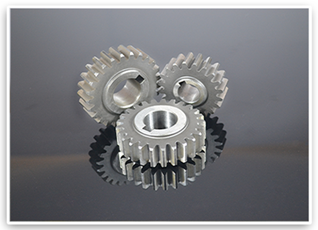
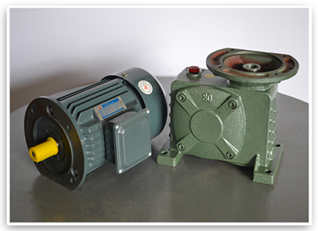
·Drive gear
The gear processing process involves the following steps: rough gear cutting - tooth surface machining - heat treatment - tooth surface grinding. The rough gear part is mainly forged, undergoing normalizing treatment to improve its machinability, facilitating cutting. Following the gear design blueprint, rough machining is performed, followed by semi-finishing, hobbing, rolling, and gear shaping to achieve basic gear formation. Subsequently, heat treatment is applied to enhance mechanical properties. As per the design requirements of the blueprint, final finishing is conducted, refining the reference and tooth profile. Through these processes, our gears achieve a grade 6 rating, boasting high wear resistance, strength, and prolonged service life.
·Power section
1. Utilizing an 80-type worm gear vertical gearbox, the gear speed converter is employed to reduce the rotational speed of the motor to the desired rate, generating a greater torque mechanism.
2. Employing a vertical motor known for its low vibration and noise levels, with the stationary rotor component featuring pure copper coils lasting ten times longer than standard coils. Equipped with ball bearings at both ends, resulting in reduced friction and lower temperatures.
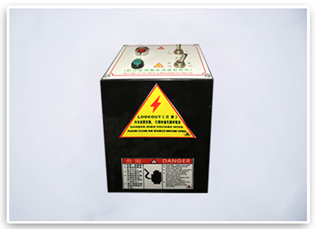
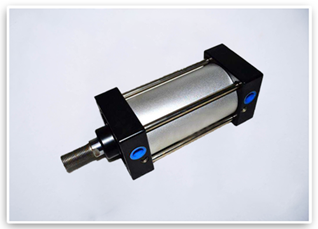
·Electric control box
1. Utilizing silver alloy relays with all-copper coils, flame-retardant safety bases ensure durability and longevity.
2. Employing safety-protected circuit delay relays with silver alloy contacts and multiple degree disks to accommodate various delay ranges.
3. Switches feature sliding contacts with self-cleaning functionality. Both normally open and normally closed contact points utilize a separate insulation structure, allowing for bipolar operation, with anti-rotation positioning and anti-loose mounting gaskets.
4. Employing self-resetting flat buttons with lightweight actuation and moderate key travel. Utilizing a modular combination structure, the contact points feature ketone-based composite material for strong conductivity, capable of carrying large currents with a lifespan of up to 1 million cycles.
·Feeder cylinder
1. Utilizing authentic Yadeke cylinders with alloy cylinder bodies, hard oxidation, and leak-proof riveting.
2. Precision CNC machining of solid aluminum, with smoothly polished inner walls, ensuring no jamming and high operational efficiency.
3. Capable of high-strength operation, durable and suitable for various working conditions.
Specification:
Type | HS-150 | HS-200 | HS-300 | HS-400 | HS-500 | HS-600 | HS-800 | |
Material Width | mm | 150 | 200 | 300 | 400 | 500 | 600 | 800 |
MaterialThickness | mm | 0.5-4.5 | 0.5-4.5 | 0.5-4.5 | 0.5-4.5 | 0.5-4.5 | 0.5-4.5 | 0.5-4.5 |
Adjusting Speed | m/min | 15 | 15 | 15 | 15 | 15 | 15 | 15 |
Motor | HP | 2 | 2 | 3 | 3 | 5 | 5 | 7.5 |
Machine L*W*H | m | 2.1*0.65*1.6 | 2.1*0.7*1.6 | 2.1*0.8*1.6 | 2.1*0.9*1.6 | 2.1*1.0*1.6 | 2.1*1.1*1.6 | 2.1*1.3*1.6 |