LH High Speed Mechanical Roller Feeder Suitable For Metal Sheet Metal Coil Width: 100.0mm~700.0mm Thickness: 0~3.5mm
-
Apply CAM mechanism
-
Reliable and stable feeding
-
One year quality guarantee
Product Description
High Speed Mechanical Roll Feeder
Structures of the machine
1. Unilateral bearing(Made in Germany)
Embedded with ultra-hard alloy and complemented by roller bearings, ensuring wear resistance, safety, high precision, and long lifespan. Gears undergo heat treatment to HRC60 and then precision grinding, ensuring high transmission accuracy.
2. Roller wheel
Utilizing hollow design, lightweight, low rotational inertia, and instant stop capability, ensuring feeding precision. Heat-treated to HRC60, chrome-plated, and then ground for high hardness, excellent wear resistance, and long lifespan.
3. Disc brakes(General brake)
Utilizes advanced clutch to ensure full contact on both sides, providing long lifespan, good stability, and high precision.
4. Reverse facing device
- Structurally similar to the unidirectional device, capable of controlling the lower roller with remarkable precision. Long-term usage does not cause any reverse movement in the lower roller, ensuring high stability and precision.
- Resistant to brake failure due to splattered oil during stamping, preventing inaccuracies in feeding distance.
- Resistant to high heat.
- Equipped with ultra-hard alloy and roller bearings for minimal wear.
- Operates with rollers moving in circular motion, avoiding jamming issues commonly associated with linear motion of four guide pillars.
- Lower friction reduces required torque, making the rotation mechanism less susceptible to damage.
- Configuration of the reverse device allows speeds up to 30 meters per minute, typically 20 meters per minute, resulting in a 50% efficiency improvement.
- Special structure enhances longevity.
Advantages
1. Continuity: Suitable for continuous processing across multiple operations.
2. High Speed: Capable of up to 600 cycles per minute.
3. Versatility: Adjustable to accommodate materials of varying widths and thicknesses, simply by adjusting the feeder to match the mold.
4. Simple, Economical, and Practical Construction.
5. Low Failure Rate and Easy Maintenance.
Form
Single Type: Used for coil materials (thickness above 0.15mm) or single and continuous stamping.
Double Type: Used for coil materials (thickness below 0.15mm), short materials, single, and continuous stamping.
Feeding accuracy
Varies depending on rotational speed and feeding length (typically within 0.03m precision). When used for positioning, precision can reach 0.01mm.
Product Description
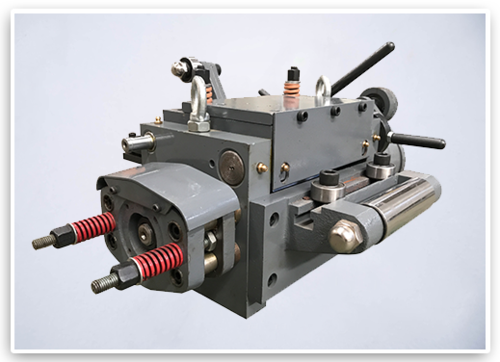
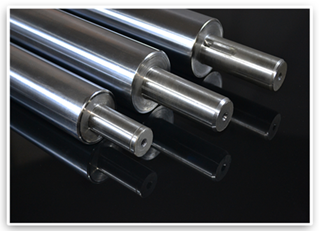
·Structures
The machine adopts a modular assembly structure, with all components fixed using high-strength screws, eliminating welding points. This facilitates future maintenance and part replacement, saving time and costs.
The left and right side plates are directly cast using liquid metal, providing excellent adaptability for various alloy formations and high flexibility.
The equipment utilizes mechanical transmission, eliminating the need for a power supply or control box.
Power is derived from the punch press output shaft, significantly reducing equipment and maintenance costs.
The overall structure is compact, occupying minimal space, and installation is simple and convenient.
·Feeding roller
1. The correction wheel is made of solid bearing steel, with thickened electroplating treatment after medium frequency heating, ensuring a surface hardness of no less than HRC58 to guarantee material durability.
2. The round steel is forged from GCr15, undergoes pre-heat treatment (spheroidizing annealing), followed by turning, milling, medium frequency treatment, rough grinding, cold stabilization, precision grinding, and finally electroplating. This process maximizes accuracy, concentricity, smoothness, and hardness, extending the service life of the correction roller.
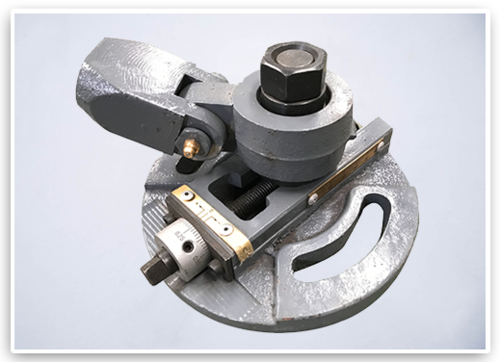
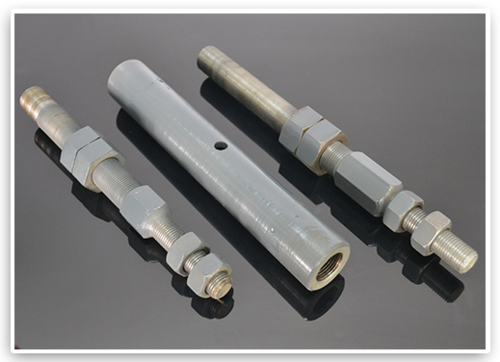
· Eccentric disc
1. Casted components provide excellent adaptability and strong flexibility, minimizing the risk of breakage.
2. Compact cross-joint connections with imported NSK bearings ensure smooth and uninterrupted operation.
3. The scale screw rod is made of high-strength material, enabling smooth adjustments.
4. The eccentric disk is equipped with multiple scales for easy adjustment.
· Pull rod
1. The middle section of the pull rod is processed from seamless pipe, ensuring high material hardness.
2. The threaded rods at both ends are machined from round steel on a lathe, ensuring proper fitting with the fixed pipe in the middle section to guarantee stability during operation.
3. The installation of the pull rod is simple, with bidirectional fixation achieved using double nuts to prevent loosening due to prolonged vibration during use, thus enhancing safety.
Specification
Model | Strip Width (mm) | Stroke.Max(mm) | Strip Thickness (mm) | Material Line Height (mm) |
LH-105NS | 100 | 50 | 0-1.6 | 55-100 |
LH-205NS | 200 | 50 | 0-1.6 | 55-100 |
LH-255NS | 250 | 50 | 0-1.6 | 55-100 |
LH-305NS | 300 | 50 | 0-1.6 | 55-100 |
LH-405NS | 400 | 50 | 0-1.6 | 55-100 |
LH-505NS | 500 | 50 | 0-1.6 | 55-100 |
LH-605NS | 600 | 50 | 0-1.6 | 55-100 |
LH-138NS | 130 | 80 | 0-1.6 | 60-120 |
LH-1310NS | 130 | 100 | 0-3.5 | 70-140 |
LH-2010NS | 200 | 100 | 0-3.5 | 70-140 |
LH-1315NS | 130 | 150 | 0-3.5 | 70-140 |
LH-2015NS | 200 | 150 | 0-3.5 | 70-140 |
LH-5010NS | 500 | 150 | 0-3.5 | 70-140 |
LH-6015NS | 600 | 150 | 0-3.5 | 70-140 |
LH-1320NS | 130 | 200 | 0-3.5 | 70-140 |
LH-2020NS | 200 | 200 | 0-3.5 | 70-140 |
LH-7020NS | 700 | 200 | 0-3.5 | 70-140 |
LH-7030NS | 700 | 300 | 0-3.5 | 100-190 |