NCHF Thin Sheet Uncoiler Straightening & Feeder 3 In 1 Machine for Applicable Sheet Thickness: 0.2mm~2.0mm
Advantages
-
PLC control
-
Servo motor drive
-
Numerical control
Product Description
· 3 In 1 NC Servo Straightener Feeder W/Uncoiler
Optimize Floor Space, Enhance Safety Coiled material travels from the uncoiler, passing through both left and right free guide rollers equipped with advanced photo sensors to maintain looping. Utilizing the opener device and bending roller system, the coiled material is fed from top to bottom, navigating through the opener device, coil tip flatness device, pinch rollers, work rollers, and feed rollers, ensuring seamless and smooth material feeding.
· STANDARD ACCESSORY:
1. Electric eye loop control system
2. Feed and straightener rolls hard chrome plated
3. Outgoing catenary to assist and support the material
4. Hold down arm device
5. Feeding line easily adjusted by advance worm gear screw jacks device
6. Uncoiler with inverter control
7. Reference indicator adjuster
8. Eccentric Roller (Upper)-easy to set up the up curve or down curve feeding exit direction
9. Hand-set coil width guide at outlet side
10. Hand-wheel-adjusted coil width guides at straightener inlet side
11. Threading table device
12. Coil tip de-bender
13. Uncoiler with air disc brake
14. A-frame type coil keeper
· OPTION:
LIHAO’S coil car
· Features
1. Versatile Operational Control: The feeder's functionalities are centralized within the PLC and a portable knob, simplifying operations for the operator. This eliminates the need for numerous function keys, ensuring efficient operation without unnecessary time wastage.
2. Enhanced Efficiency and Safety: Mechanized actions replace manual operations, significantly reducing time wastage and boosting work efficiency. Moreover, the feeder is equipped with various auxiliary functions for material feeding and support, minimizing operator proximity to materials for enhanced safety.
3. Convenient Control Options: Users have the flexibility to switch between punch master and device master modes as per their requirements. This versatility maximizes the device's adaptability and offers cost savings for users.
4. Optimal Footprint: Despite the robust capabilities of the Lihao NCHF series, its form factor is designed to occupy the most rational space in the industry. This ensures optimal utilization of site resources while minimizing costs.
5. Comprehensive Control System Compatibility: The NCHF series integrates a complete set of Japanese Mitsubishi control systems, ensuring compatibility with various domestic and international standards. Users can operate the equipment directly without concerns about data conversion or compatibility issues.
6. Thoughtful Design: Introducing industrial design principles, the NCHF series prioritizes both performance and aesthetics. This design approach enhances equipment visibility and improves operational comfort while maintaining fundamental performance standards.
Structure
· Material part
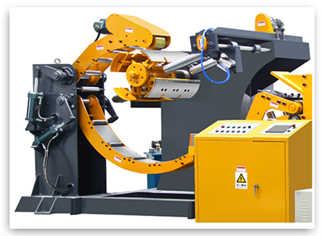
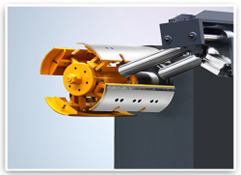
The frame component of the material frame is constructed from Q235B, chosen for its notable elongation, robust strength, and resilience, making it ideal for punching and welding in the fabrication of general mechanical parts. Q235B material undergoes laser cutting to ensure overall plate flatness. Following straight cutting, CNC machining is employed to ensure precise hole positioning. Subsequently, CO2 protection welding is utilized to secure the rack's dimensions after hole processing. Finally, annealing heat treatment is applied to modify the internal steel structure, enhancing steel performance. This heat treatment process not only fortifies the metal material to maximize its potential performance but also reduces structural weight, improves mechanical product quality, and significantly prolongs machine part service life. Additionally, it eradicates welding process defects, diminishes segregation, alleviates internal stress, and promotes uniformity in steel structure and properties.
· Material spindle
The spindle bearing bore is meticulously crafted using a horizontal boring machine, ensuring a coaxiality precision of less than 0.015mm. For the main shaft of the material frame, 40Mn tube forging is employed. Through processes of spheroidizing annealing, quenching, and tempering, the main shaft's flexibility is significantly enhanced, surpassing that of typical carbon steel pipes commonly utilized in the industry. This enhancement optimizes the load-carrying capacity of the spindle, facilitating smoother coil starts and stops while reducing motor load.
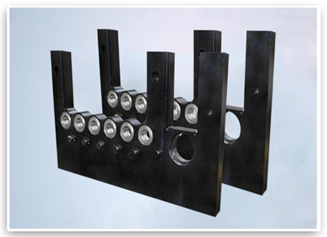
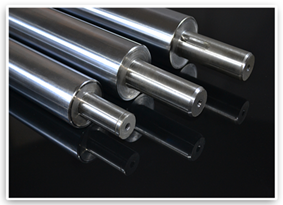
· Left and right vertical board
The left and right vertical plates of the straightening head are crafted from cast steel ZG25, renowned for its exceptional strength, plasticity, toughness, and welding capabilities, ensuring minimal deformation and high stability. Each set of equipment's left and right vertical plates undergo precision molding, followed by casting with ZG25. Subsequently, annealing is applied, subjecting the material to prolonged high temperatures and gradual cooling. This process serves to rectify or eliminate structural defects and residual stresses inherent in steel due to casting, forging, rolling, and welding processes. Its primary objectives include preventing workpiece deformation and cracking, facilitating workpiece softening for machining, refining grains, and enhancing structure to improve mechanical properties. Through CNC machining, the accuracy of the vertical plate holes and overall stability is meticulously maintained.
· Correct roller part
The correction roller stands as the pivotal component within the Uncoiler, Straightener, Feeder, 3 in 1 setup. In Lihao Machinery's processing approach, GCr15 round steel serves as the foundation material, initially forged into shape. The roller undergoes a series of meticulous treatments, commencing with pre-heat treatment via spheroidizing annealing, followed by stabilization through carburization, milling, intermediate frequency treatment, coarse grinding, and deep cooling. Subsequent refinement processes ensue, culminating in plating. This comprehensive treatment regimen ensures optimized accuracy, concentricity, finish, and hardness, effectively prolonging the correction roller's operational lifespan.
· Gear section
Lihao Machinery employs a meticulous gear machining process, which involves several key steps:
1. Gear Grinding Processing: Initial shaping of the gear profile.
2. Tooth Surface Processing: Refinement of tooth surface geometry.
3. Heat Treatment: Enhancement of mechanical properties through heat treatment.
4. Tooth Surface Finish Grinding: Finalization of tooth surface smoothness.
For gear components, forging is the primary method, followed by normalizing treatment to improve machinability. Gears are then crafted according to precise drawings, progressing through roughing, semi-finishing, rolling, and gear shaping stages to achieve near-final form. Subsequent heat treatment optimizes mechanical properties. Finally, according to design specifications, the gears undergo final finishing and tooth profiling. This comprehensive approach yields gear ratings of up to grade 6, ensuring exceptional wear resistance, high strength, and extended service life.
· Specification:
Model | NCHF-300B | NCHF-400B | NCHF-600B |
Coil Width | 50-400m | 50-600mm | 50-800mm |
Coil Thickness | 0.2-2.0mm | ||
Straight Performance(Width*Thickness) |
300*1.4mm 250*1.6mm 190*2.0mm |
400*1.2mm 300*1.4mm 250*1.6mm 190*2.0mm |
600*0.8mm 500*1.0mm 400*1.2mm 300*1.4mm 250*1.6mm 190*2.0mm |
Coil.I.Dia | 460-530mm | ||
Coil.O.Dia | 1200mm | ||
Load Weight | 3000KG | ||
Straightener Roll (Qty) | Φ48mm*11 (upper*6/lower*5) | ||
Uncoiler Motor | 1.5KW | ||
Straightener Motor | 2.9KW | ||
Speed Range | 0~20m/min | ||
Feed Pitch Accuary | <±0.2mm | ||
Feed Leveler | 1000-1150mm | ||
Power | AC 380V,3 Phase, 50HZ | ||
Air Supply | 0.5 Mpa |
· Electronic control configuration table:
Number |
Name |
Brand |
1 |
servo motor |
Yaskawa |
2 |
7 inch human-machine interface |
Mitsubishi |
3 |
4.3 inch human-machine interface |
Mitsubishi |
4 |
Conventional motor |
Taiwan TECO |
5 |
Frequency converter |
Taiwan DELTADELTA
|
6 |
Pneumatic Components |
SMC |
7 |
PLC |
Mitsubishi |
8 |
Relay components, etc. |
Schneider |
9 |
power cable |
Baosheng cable(Flame retardant) |
· Hydraulic station configuration table:
Number |
Name |
Model |
Amount |
Brand |
1 |
Lifting cylinder |
NCLF-1.6.4 |
1 |
Wuqiang |
2 |
Overflow valve |
RVP-02-LC |
1 |
Dengsheng |
3 |
Electromagnetic reversing valve |
D4-02-2M3M-A2 |
1 |
Dengsheng |
4 |
Clamping cylinder |
NCLF--1.4.6 |
1 |
Wuqiang |
5 |
Rotary joint |
NCLF-1.4.5 |
1 |
New Ma Tai |
6 |
Hydraulic control check valve |
PCVA-02-A |
1 |
Dengsheng |
7 |
Electromagnetic reversing valve |
D4-02-3C4-A2 |
1 |
Dengsheng |
8 |
Oil motor |
OMP-160 |
1 |
Danfoss |
9 |
Brake valve |
MMR-01-C-30 |
1 |
Yuci |
10 |
One-way throttle |
TVCW-02-I-V |
2 |
Dengsheng |
11 |
Electromagnetic reversing valve |
D4-02-3C2-A2 |
2 |
Dengsheng |
12 |
Pressure gauge switch |
KF-L8/14E |
1 |
Liming |
13 |
Pressure gauge |
W2 1/2-250 |
1 |
Dengsheng |
14 |
Substrate |
NMC-01-4-00 |
1 |
Yuci |
15 |
Check valve |
OH-03-A1 |
1 |
Dengsheng |
16 |
Oil filter |
MF-06 |
1 |
Dengsheng |
17 |
Oil pump |
RA7RD66 |
1 |
Dengsheng |
18 |
Motor |
CT-08-5HP-4P-3J-V |
1 |
Dengsheng |
19 |
Liquid level thermometer |
LS-3 |
1 |
Dengsheng |
20 |
air filter |
HS-1162 |
1 |
Dengsheng |
· Applications
The NC Feeder is suitable for high-speed fixed rotor stamping production lines, heat exchanger stamping production lines, brake pad and friction sheet production lines, hardware parts stamping production lines, radiator production lines, new energy battery shell stamping line, and more.
· Package
Based on the specific characteristics of different products, packaging should be as follows, if necessary:
· Lihao Pre-sales Service
1. Custom 3-in-1 coil feeding line machinery: Based on the technical parameters of the application-related equipment provided by the customer, we can modify our machines to meet the customer's convenience and high production efficiency.
2. Solution Design: According to the customer's product processing requirements, we design unique solutions to support higher manufacturing efficiency and better processing quality.
· Lihao After-sales Service
1. As a professional manufacturer and supplier of automation machines, LIHAO provides English training videos and user manuals for uncoiler straightener feeder 3 in 1 coil feed line machines, covering installation, operation, maintenance, and troubleshooting. Additionally, we offer technical guidance through remote means such as TeamViewer, email, mobile, WhatsApp, Skype, and 24/7 online chat when you encounter issues with installation, operation, or adjustments.
2. Customers can choose to come to our factory for 2-5 days of training. We will provide professional guidance and effective face-to-face training.
3. Our engineers will provide on-site guidance and training services at your location. We will require your assistance in arranging visa procedures, prepaying travel expenses, and accommodating us during the business trip and service period.
· Lihao Automation Feeder Machine Guarantee
1. The entire coil feeder lines machine is covered by a 1-year free warranty.
2. Lifetime maintenance is provided, with our after-sales department offering 24/7 online support.
3. We offer machine-related parts services. After the 1-year warranty period, buyers will need to pay for repair parts.
· Shipping to Around the World
The uncoiler straightener feeder 3 In 1 machines can be shipped worldwide via sea, air, or express logistics through DHL, FedEx, and UPS. You are welcome to obtain a free quote by filling out the form with your name, email, product, and requirements. We will promptly contact you with complete information, including the most suitable delivery method (fast, secure, discreet) and shipping costs.