NCLF Super Thick Sheet Uncoiler Straightening Feeder 3 In 1 Machine For Applicable Sheet Thickness: 2.0mm~9.0mm
Share
PLC control
Servo motor drive
Numerical control
Product Description
3 In 1 NC Servo Straightener Feeder W/Uncoiler
Maximize Looping Space, Enhance Safety. Initiating from the uncoiler, the coiled material navigates through left and right free guide rollers, aided by advanced photo sensors for precise looping. Progressing downwards through the opener device and bending roller system, it traverses a pathway comprising the opener device, coil tip flatness device, pinch rollers, work rollers, and feed rollers, ensuring impeccably smooth material feeding.
STANDARD ACCESSORY:
Electric eye loop control system
Feed and straightener rolls hard chrome plated
Hold down arm device
Feeding line easily adjusted by advance worm gear screw jacks device
Uncoiler with inverter control
Pneumatic threading tables devices provided at uncoiler and straightener
Hand-set coil width guide at outlet side
Hand-wheel-adjusted coil width guides at straightener inlet side
Reference indicator adjuster
Coil tip flattener
Uncoiler with air disc brake
Coil keeper
OPTION:
LIHAO’S coil car
Shearing device
Features
1. Streamlined Operation: All feeder functions are consolidated within the PLC and a portable knob, simplifying operation for the user. No need to fret over excessive function keys or waste time navigating them.
2. Enhanced Efficiency and Safety: Mechanical actions replace manual operations, reducing unnecessary delays and enhancing work efficiency. With numerous auxiliary functions for material feeding and support, operators can maintain a safe distance from the materials, maximizing safety.
3. Versatile Control Options: Users can effortlessly switch between punch master and device master modes based on their requirements, optimizing device adaptability and reducing costs.
4. Optimal Footprint: While Lihao NCLF series are powerful, the form factor are also the most reasonable in the industry, which can maximize the cost of the site.
5. Strong Control System Compatibility: The NCLF series integrates Japanese Mitsubishi control systems, ensuring compatibility with various international standards. Users can operate seamlessly without worrying about data conversion or other compatibility issues.
6. Thoughtful Design: Introducing industrial design elements, the NCLF series prioritizes equipment visibility and operator comfort while maintaining exceptional performance standards.
Structure
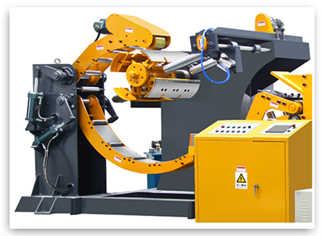
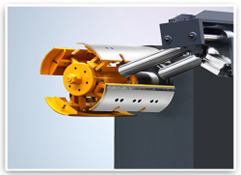
·Material part
The frame section of the material rack is constructed using Q235B steel, renowned for its elongation, robust strength, and toughness, making it a staple in the fabrication of general mechanical components. Employing laser cutting techniques ensures the overall flatness of the plate, while CNC machining guarantees precise hole positioning. Subsequently, CO2 protection welding is utilized to secure the rack's dimensions post-hole processing. Through annealing heat treatment, the internal structure of the steel undergoes modification, enhancing its performance. This heat treatment not only fortifies the metal material, optimizing its potential performance, and reducing structural weight but also elevates the quality of mechanical products, significantly extending the lifespan of machine parts. Moreover, it serves to rectify welding-induced defects, mitigate segregation, alleviate internal stresses, and foster uniformity in the steel's structure and properties.
·Material spindle
The spindle bearing bore is meticulously crafted using a horizontal boring machine, ensuring a coaxiality below 0.015mm. For the main shaft of the material frame, 40Mn tube forging is employed. Following spheroidizing annealing and quenching and tempering treatment, the main shaft exhibits remarkable flexibility, surpassing that of conventional carbon steel pipes prevalent in the industry. This enhancement optimizes the spindle's load-bearing capacity, facilitating smoother coil starting and stopping while reducing motor load.
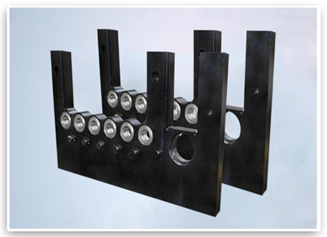
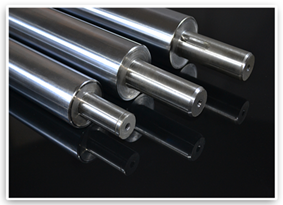
·Left and right vertical board
The vertical plates on both sides of the straightening head are crafted from cast steel ZG25, renowned for its exceptional strength, plasticity, and toughness, along with excellent welding capabilities. Each set of equipment undergoes a meticulous process: first, molds are employed to shape the left and right vertical plates, which are then cast using ZG25. Subsequently, annealing is applied, subjecting the material to prolonged exposure to high temperatures followed by gradual cooling. This annealing process serves multiple purposes: rectifying or eliminating various structural flaws and residual stresses resulting from steel casting, forging, rolling, and welding processes; safeguarding against deformation and fractures of the workpiece; facilitating workpiece softening for easier cutting; refining grain structure; and enhancing mechanical properties. Additionally, CNC machining ensures precise boring of holes in the vertical plates, guaranteeing accuracy and stability.
·Correct roller part
The correction roller serves as the central component within the Uncoiler, Straightener, Feeder, 3-in-1 setup. At Lihao Machinery, we employ a meticulous processing technique. We start by forging round steel into shape using GCr15 steel. This steel undergoes a series of steps to ensure optimal performance and longevity. Initially, it undergoes pre-heat treatment, specifically spheroidizing annealing, which prepares it for further processing.
Following annealing, the steel is stabilized through a sequence of procedures including carburization, milling, intermediate frequency treatment, coarse grinding, and deep cooling. This comprehensive treatment enhances the roller's accuracy, concentricity, surface finish, and hardness.
To further augment its durability, the roller undergoes refining processes before being plated. This final step not only extends the lifespan of the correction roller but also enhances its overall performance.
·Gear section
At Lihao Machinery, our gear machining process is meticulously crafted to ensure optimal performance and longevity. Here's an overview:
We begin with gear grinding processing, followed by tooth surface processing, heat treatment, and tooth surface finish grinding. Forging is predominantly utilized for gear components, with subsequent normalizing treatment to enhance machinability.
The gear manufacturing process follows a systematic approach: starting with design interpretation and blueprinting, we proceed to roughing, semi-finishing, and then conduct carburization, rolling, and gear shaping to achieve the desired gear shape.
Once the basic form is achieved, heat treatment is employed to enhance mechanical properties. Subsequently, we refine the gears according to design specifications, focusing on final finishing, benchmarking, and tooth type finishing.
Following this comprehensive treatment, our gears attain a grade 6 rating, characterized by high wear resistance, superior strength, and an extended service life.
Model | NCLF-600B | NCLF-800B | NCLF-1000B | NCLF-1300B |
Coil Width | 70-600m | 70-800mm | 70-1000mm | 70-1300mm |
Coil Thickness | 2.0-9.0mm | |||
Straight Performance(width*thick) |
600*5.0mm 450*6.0mm 330*7.0mm 250*8.0mm 200*9.0mm |
800*4.5mm 600*5.0mm 450*6.0mm 330*7.0mm 250*8.0mm 200*9.0mm |
1000*4.0mm 800*4.5mm 600*5.0mm 450*6.0mm 330*7.0mm 250*8.0mm 200*9.0mm |
1300*3.2mm 1000*4.0mm 800*4.5mm 600*5.0mm 450*6.0mm 330*7.0mm 250*8.0mm 200*9.0mm |
Coil.I.Dia | 460-530mm | |||
Coil.O.Dia | 1400mm | |||
Load Weight | 5000KG | 7000KG | 7000KG | 7000KG |
Straightener Roll (Qty) | Φ136mm×7 (upper*4/lower*3) | |||
Feed Roll | Φ152mm | |||
Uncoiler Motor | 2.2KW | 3.7KW | 3.7KW | 3.7KW |
Straightener Motor | 15KW | 22KW | ||
Speed Range | 0-20m/min | |||
Feed Pitch Accuary | <±0.2mm | |||
Feed Leveler | 1050-1250mm | |||
Power | AC 380V,3 Phase, 50HZ | |||
Air Supply | 0.5Mpa |
Electronic control configuration table:
Number |
Name |
Brand |
1 |
servo motor |
Yaskawa |
2 |
7 inch human-machine interface |
Mitsubishi |
3 |
4.3 inch human-machine interface |
Mitsubishi |
4 |
Conventional motor |
Taiwan TECO |
5 |
Frequency converter |
Taiwan DELTADELTA
|
6 |
Pneumatic Components |
SMC |
7 |
PLC |
Mitsubishi |
8 |
Relay components, etc. |
Schneider |
9 |
power cable |
Baosheng cable(Flame retardant) |
Hydraulic station configuration table:
Number |
Name |
Model |
Amount |
Brand |
1 |
Lifting cylinder |
NCLF-1.6.4 |
1 |
Wuqiang |
2 |
Overflow valve |
RVP-02-LC |
1 |
Dengsheng |
3 |
Electromagnetic reversing valve |
D4-02-2M3M-A2 |
1 |
Dengsheng |
4 |
Clamping cylinder |
NCLF--1.4.6 |
1 |
Wuqiang |
5 |
Rotary joint |
NCLF-1.4.5 |
1 |
New Ma Tai |
6 |
Hydraulic control check valve |
PCVA-02-A |
1 |
Dengsheng |
7 |
Electromagnetic reversing valve |
D4-02-3C4-A2 |
1 |
Dengsheng |
8 |
Oil motor |
OMP-160 |
1 |
Danfoss |
9 |
Brake valve |
MMR-01-C-30 |
1 |
Yuci |
10 |
One-way throttle |
TVCW-02-I-V |
2 |
Dengsheng |
11 |
Electromagnetic reversing valve |
D4-02-3C2-A2 |
2 |
Dengsheng |
12 |
Pressure gauge switch |
KF-L8/14E |
1 |
Liming |
13 |
Pressure gauge |
W2 1/2-250 |
1 |
Dengsheng |
14 |
Substrate |
NMC-01-4-00 |
1 |
Yuci |
15 |
Check valve |
OH-03-A1 |
1 |
Dengsheng |
16 |
Oil filter |
MF-06 |
1 |
Dengsheng |
17 |
Oil pump |
RA7RD66 |
1 |
Dengsheng |
18 |
Motor |
CT-08-5HP-4P-3J-V |
1 |
Dengsheng |
19 |
Liquid level thermometer |
LS-3 |
1 |
Dengsheng |
20 |
air filter |
HS-1162 |
1 |
Dengsheng |