STL Series Two-Stage Sheet Roller Precision Straightening Machine: Metal Sheet Leveling For Material Thickness Range Of 0.15mm - 0.6mm
Share
For different thickness material continuous punching use
Work together with uncoiler machine for automatic production
Can be customized
Product Description
Feature:
1. This series of straightening machines is specifically designed for medium-thickness material products requiring high precision stamping. It is well known that without leveling and stress relief of coil materials, it is impossible to produce high-quality products. Therefore, the performance of straightening machines plays a crucial role in production.
2. Due to variations in curvature at different points of the material, a single arrangement of straightening rollers cannot meet the high-precision straightening requirements. The STL series innovatively adopts a concept of coarse straightening with large roller spacing followed by fine straightening with small roller spacing, achieving various arrangements to meet customer stamping requirements.
3. The straightening rollers and auxiliary rollers of this machine are all made of imported SUJ2 material, heat-treated to HRC60°, ground, and then ground again after hard chrome plating to ensure uniform hard chrome layer and shape tolerance of each shaft.
4. Both coarse and fine straightening adjustments of this machine employ floating four-point balance fine-tuning devices, equipped with a dial gauge for quickly finding the leveling point.
5. The machine adopts universal joint drive and full gear transmission, suitable for products requiring high straightening precision.
6. The entire machine uses high-precision bearings and is equipped with a lubrication system to extend its lifespan.
7. Each straightening roller of the S series precision straightening machine is equipped with leveling auxiliary rollers to ensure that they do not bend or deform during production, thereby improving the flatness quality of the products.
8. Both upper and lower auxiliary rollers are fixed to enhance their rigidity and prevent deformation under stress.
9. Due to differences in material, width, and thickness, there is no unified numerical reference. Therefore, it is recommended to try straightening small sections of material before continuous production once the desired effect is achieved.
10. Two-stage straightening, purchasing two straightening machines at once for enhanced performance.
Introduction:
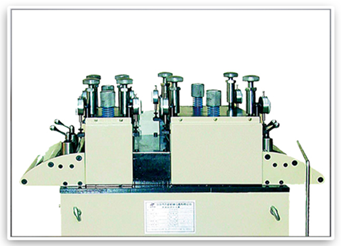
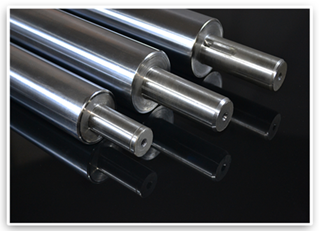
·Leveling head
1. The machine head adopts a parallel roller design with a total of 19 precision straightening rollers, 9 on the upper side and 10 on the lower side.
2. Utilizing a four-point fine-tuning mechanism, it is more suitable for processing high-precision products. The entry and exit of materials are controlled by four independently adjustable pressure wheels, effectively preventing material deviation and deformation.
3. The material support rollers feature non-powered galvanized steel drums, ensuring durability with their integrated material construction. Equipped with mechanical bearings, they offer flexible rotation and long-lasting performance.
4. Employing cast iron handwheels with surface electroplating treatment, representing a classic and traditional design.
5. Protective covers are installed on both sides of the transmission part, equipped with viewing windows for convenient observation.
·Leveling wheel
1. The straightening rollers are made of solid bearing steel, undergo thick electroplating treatment after medium-frequency processing, ensuring a surface hardness of no less than HRC58 to guarantee material durability.
2. GCr15 steel is forged into round bars, subjected to preheating treatment (spheroidizing annealing), followed by turning, milling, medium-frequency processing, rough grinding, cold stabilization, and finally precision grinding. This process maximizes precision, concentricity, surface finish, and hardness, thereby extending the service life of the straightening rollers.
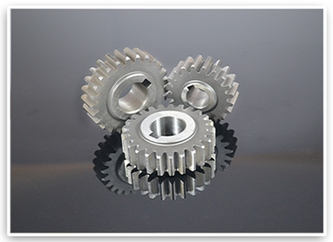
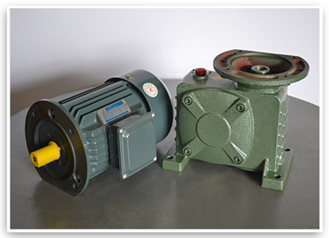
·Transmission gear
The gear manufacturing process consists of the following stages: gear grinding, tooth surface machining, heat treatment, and tooth surface finishing. The initial gear components are primarily produced through forging, which undergoes normalization to enhance machinability and cutting properties. Following the gear design specifications, rough machining is conducted, followed by semi-finishing, hobbing, and gear shaping to achieve the desired gear form. Subsequently, heat treatment is applied to enhance mechanical properties. As per the design requirements, final finishing, benchmarking, and tooth profiling are carried out. Upon completion of these processes, our gears achieve a grade rating of 6, characterized by high wear resistance, superior strength, and prolonged lifespan.
·Power section
1. Employing the 80-type worm gear vertical gearbox, the motor facilitates the conversion of rotational speed through the gear speed converter. This process decelerates the motor's rotations to the desired level, generating a mechanism with significant torque.
2. Utilizing a vertical motor characterized by minimal vibration and noise, the fixed rotor section features pure copper coils, offering a lifespan ten times longer than conventional coils. Equipped with ball bearings at both ends, the motor experiences low friction and operates at lower temperatures.
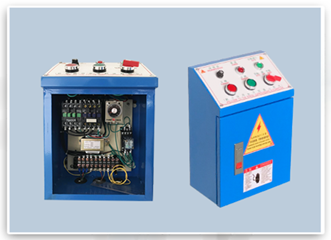
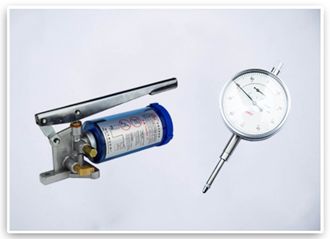
·Electrical control box
1. Utilizes silver alloy relays, all-copper coils, and flame-retardant safety bases for enhanced durability and longevity.
2. Employs safety-protected circuit delay relays featuring silver alloy contacts and multiple-degree disks to accommodate various delay requirements.
3. Switches with sliding contacts incorporate self-cleaning functionality, with both normally open and normally closed contacts utilizing edge-point structures. Equipped with anti-rotation positioning and anti-loose mounting gaskets for enhanced stability.
4. Incorporates self-duplex flat button switches designed for light operation and moderate keystrokes. Utilizes a building block combination structure and ketone-based composite points for high conductivity, capable of enduring 1 million cycles of use.
·Dial indicator, yellow oil pump
1. Adopts a manual grease pump for faster and more labor-saving oil dispensing, with imported oil seals to prevent oil leakage, and imported springs resistant to deformation and aging.
2. Utilizes a steel percentage gauge with a precision dial, dust-proof glass, internal copper lining, and a copper-based movement for stable structure and accurate measurement.
Parameter:
Model | STS-100 | STS-200 | STS-300 | STS-400 |
Max width(mm) | 150 | 200 | 300 | 350 |
Thickness(mm) | 0.4-2.2 | 0.4-2.2 | 0.4-2.2 | 0.4-2.2 |
Speed(m/min) | 16 | 16 | 16 | 16 |
Motor(Hp) | 1HP×4P | 2HP×4P | 2HP×4P | 3HP×4P |
Coarse diameter correction | Φ45 | Φ45 | Φ45 | Φ45 |
Coarse pose number | 2/3(Up/down) | 2/3(Up/down) | 2/3(Up/down) | 2/3(Up/down) |
Precise diameter Leveling | Φ34 | Φ34 | Φ34 | Φ34 |
Precise leveling wheels | 7/8(Up/down) | 7/8(Up/down) | 7/8(Up/down) | 7/8(Up/down) |
Dimension(m) | 1.6×1.0×1.5 | 1.6×1.05×1.5 | 1.6×1.15×1.5 | 1.6×1.2×1.5 |