What is a Pneumatic Punch Press?
A pneumatic punch press is an automated machine tool equipped with a programmable control system, utilized for processing various metal sheet components. It efficiently completes multiple complex perforations and shallow stretching operations in a single cycle, automatically processing holes of different shapes and dimensions as required. Understanding the working principles, processing methods, selection techniques, operational guidelines, and maintenance essentials of pneumatic punch presses is crucial.
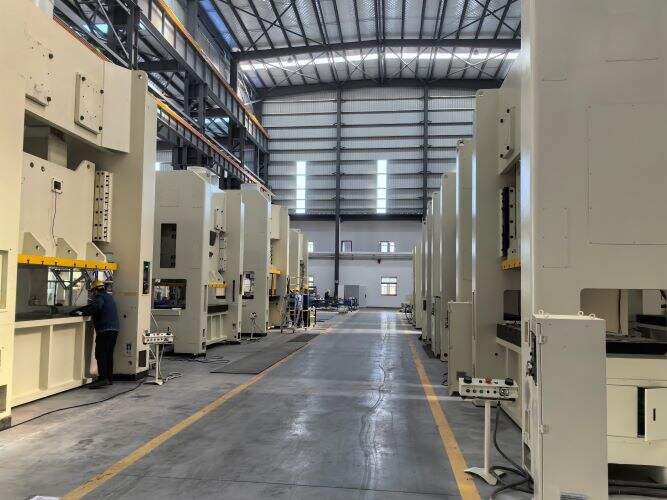
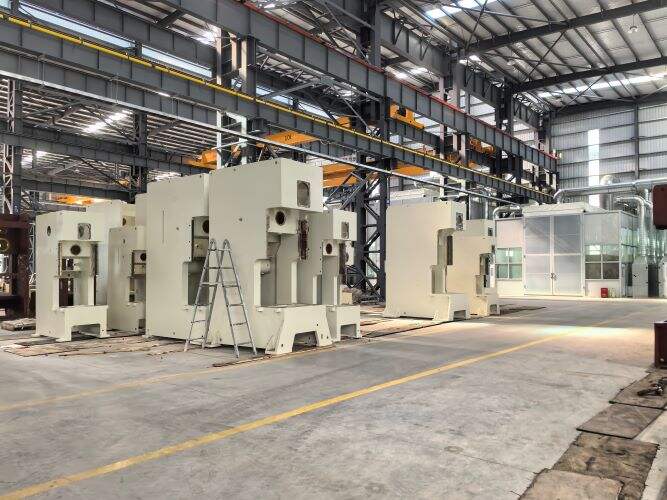
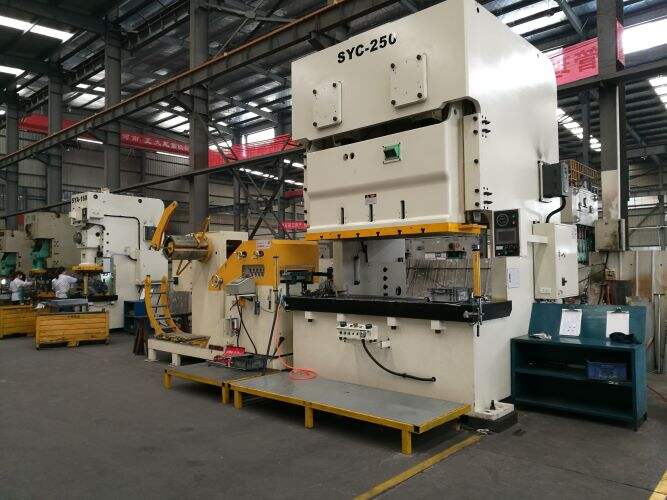
Working Principles of a Pneumatic Punch Press
The design principle of a pneumatic punch press involves converting rotary motion into linear motion. The primary output is driven by the main electric motor, which powers the flywheel. The clutch, in turn, engages gears, crankshafts (or eccentric gears), connecting rods, and other components, achieving the linear motion of the slide. The motion from the main electric motor to the connecting rod involves circular motion.
The pneumatic punch press exerts pressure on the workpiece to deform it, achieving the desired shape and precision. This process requires the collaboration of a set of dies (upper and lower) between which the material is placed. The force applied to the material during processing is absorbed by the mechanical body of the pneumatic punch press, resulting in the press's motion and the production of the part.
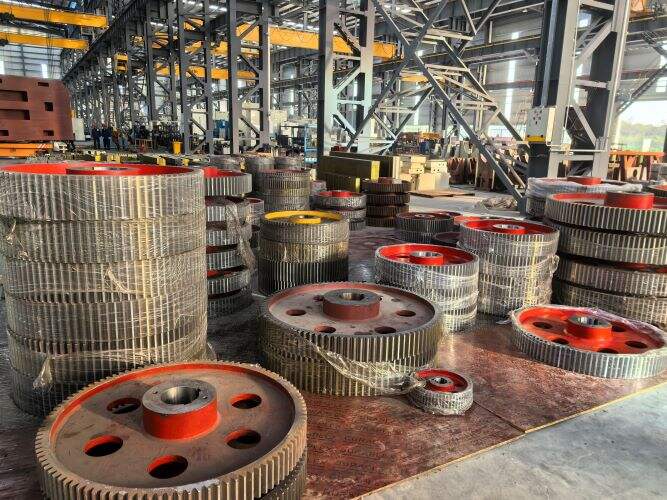
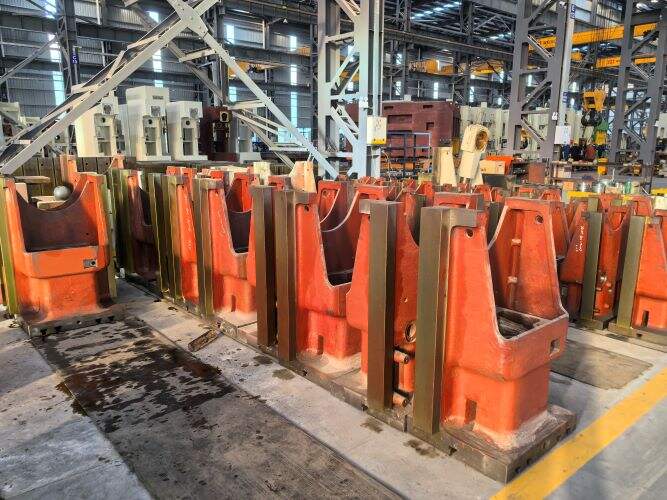
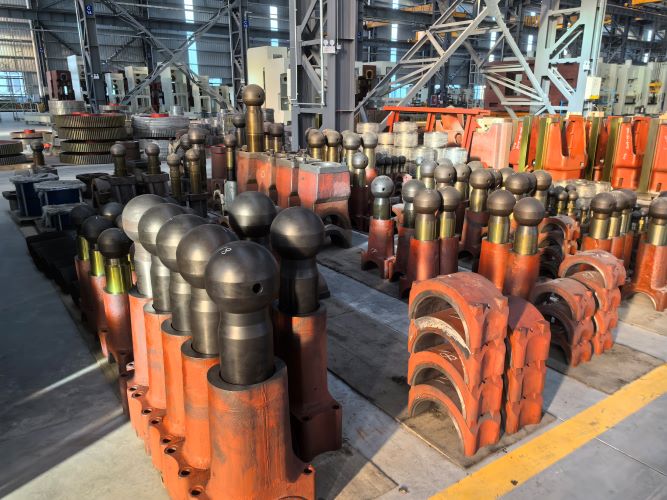
Processing Methods of a Pneumatic Punch Press
1. Single Stroke: Completes a single punching operation, including linear distribution, arc distribution, circumferential distribution, and grid hole stamping.
2. Continuous Shearing in the Same Direction: Utilizes a stacking method with rectangular dies to process long holes, cut edges, and more.
3. Continuous Shearing in Multiple Directions: Employs smaller dies for processing larger holes.
4. Nibbling: Employs small circular dies to consecutively punch and shape arcs.
5. Single Forming: One-time shallow stretching forming based on the shape of the dies.
6. Continuous Forming: Larger than standard dies, used for forming processes such as large standard louvers, embossing, and forming steps.
7. Array Forming: Processing multiple identical or different workpieces on a large sheet.
Selection Techniques for a Pneumatic Punch Press
1. Consider the length, material thickness, production output, and available space when choosing a pneumatic punch press for specific requirements.
2. Evaluate whether additional features, such as a coil cart for easy loading or a loop control system for tension management, are required for the application.
Operational Safety Guidelines for a Pneumatic Punch Press
1. Ensure that the power sockets for the machine body and control box do not exceed the specified load.
2. Prior to operation, check the lubrication of the moving parts and inspect the clutch and brake for proper functioning.
3. During die replacement, close the power supply, ensure the machine stops completely, and only then install and adjust the dies.
4. Before starting the pneumatic punch press, ensure that the work area is clear of personnel and debris.
5. During machine operation, refrain from inserting hands into the working area, and never manually handle or remove workpieces.
6. Emergency stop buttons should be used when manually feeding or assisting in feeding during the punching process.
7. If abnormal noises or mechanical malfunctions are detected, promptly shut off the power and conduct a thorough inspection.
Maintenance Tips for a Pneumatic Punch Press
1. Keep the central column and slide guide clean to prevent scratches and maintain platform cleanliness during die installation.
2. Lubricate the flywheel and feeder monthly with grease for optimal machine performance.
3. Change the machine oil (32# mechanical oil or Mobil 1405#) within the first month of use and subsequently every six months to ensure normal operation and precision.
Understanding these aspects of pneumatic punch presses is essential for maximizing efficiency, safety, and the lifespan of the equipment in various metalworking applications.