DBMT Double-Head Uncoiler with Speed Control Box for Metal Sheets , Decoiler Suitable for Material Widths 200mm - 400mm
Share
Hydraulic expansion of the mandrel ( for 3 ton above uncoiler )
Pneumatic coil hold down arm ( for 1.6mm above thickness )
Double head rotation by foot pedal
Features
1.Save material changing time, improve production efficiency
2.Can work with straightener.
3.Can be changed to motorized by add motor and control box.
4.With manual and hydraulic two kinds of expansion type.
5.This machine is suitable for high speed punching, such as stator, rotor and ET sheet, etc.
Product Description
Motorised Double Head Uncoiler
Machine Struture:
1.A coil keeper
2.Tiles
3.Connecting rod
4.Adjusting screw
5.Adjusting handle
6.Hand wheel
Features:
1. Save material changeover time and enhance production efficiency.
2. Can be used in conjunction with a straightening machine.
3. Can be equipped with a motor and electronic control to become a powered material rack.
4. Offers two expansion methods: manual hand crank expansion and hydraulic expansion.
5. For narrow materials, customizations for left and right shifting are available.
6. This machine is suitable for high-speed stamping, such as stators, rotors, and ET sheets.
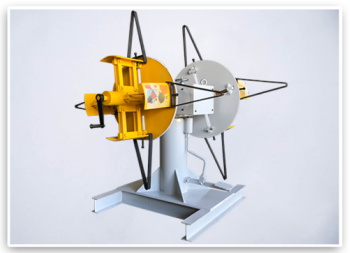
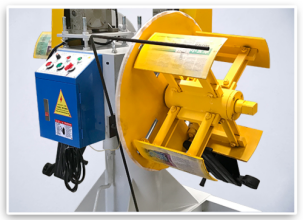
Body structure
1. This machine consists of a frame, a main spindle housing, and a material loading rack. The main spindle housing serves as the carrier, supported by a long wheelbase, offering compact size, minimal footprint, high load-bearing capacity, and flexible usage.
2. With a dual-axis structure, it allows for loading material while in operation, greatly reducing material changeover time, enhancing production capacity, and lowering production costs.
3. The equipment comes in both powered and non-powered versions, and can be used in conjunction with adjusting straighteners and stock straighteners.
Main shaft and tile
1. The tiles are made of A3 material, undergo deburring after cutting, followed by milling of tile chamfers, and then proceed to bending, drilling, and milling groove processes.
2. Anti-slip nuts are used to secure all components, preventing loosening during operation, thereby avoiding machine damage or injury incidents.
3. Both the main spindle screw and screw sleeve are precision machined to ensure smooth adjustment of the machine's inner and outer diameters, thus avoiding unnecessary downtime for adjustments.
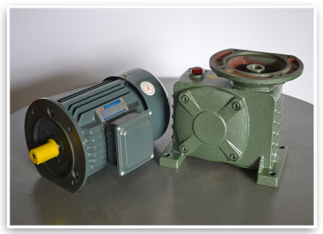
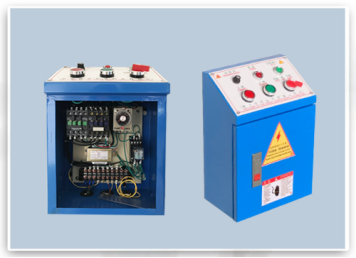
Power part
1. Employing an 80-type worm gear vertical reducer, utilizing the gear speed converter, to reduce the rotation speed of the motor to the desired speed and achieve a mechanism with higher torque.
2. Utilizing a vertical motor, with low vibration and noise. The stator part adopts pure copper coils, with a lifespan ten times that of ordinary coils. Equipped with ball bearings at both ends, resulting in low friction and temperature.
Electric control box
1. Utilizing silver alloy relays, all-copper coils, flame-retardant safety bases, ensuring long-lasting durability.
2. Equipped with safety protection adjustable circuit delay relays, silver alloy contacts, multiple andrums, meeting various delay ranges.
3. Switches feature sliding contacts with self-cleaning function. Normally open and normally closed contacts adopt a split-coupled structure, allowing bipolar operation, with anti-rotation positioning and anti-loosening mounting pads.
4. Utilizing self-resetting flat buttons, light and agile in operation, with moderate keystroke. The contact blocks employ ketone-based composite points, providing strong conductivity and capable of carrying large currents, with a lifespan of up to 1 million cycles.
The base part
1. The frame is designed with welded construction, utilizing dual protection welding machines for welding. Welding starts with welding the vertical corners, followed by welding the flat corners. Short seams are welded first, followed by long seams, ensuring tight welds and enhancing quality.
2. All frame materials are cut using laser or plasma cutting, resulting in high precision.
3. All parts are machined using CNC and numerical control technology, ensuring good interchangeability of equipment.
4. The overall structure is simple, allowing assembly and replacement of equipment parts by general technical workers, making it convenient and quick, significantly reducing maintenance costs.
Type | Material width (mm) | Coil.I.Dia (mm) | Coil.O.Dia (mm) | Coil Weight (kg) |
DBMT-200 | 200 | 450-530 | 1200 | 500 |
DBMT-300 | 300 | 450-530 | 1200 | 800 |
DBMT-400 | 400 | 450-530 | 1200 | 1000 |
DBMT-500 | 500 | 450-530 | 1200 | 1500 |
Option:
Hydraulic expansion of the mandrel ( for 3 ton above uncoiler )
Pneumatic / hydraulic coil hold down arm (for 1.6mm thickness above )
AC variable speed drives
Motorized double head rotation (by hydraulic motor)
Load coil car
Note: Custom engineering can be provided to meet any application demands.